Performance development of motor fan aerodynamic noise analysis simulation
Undertake noise analysis and simulation, NVH noise optimization design and performance development for fans and blowers, covering fields such as industrial fans and blowers, automotive wind noise, industrial motors, household appliances, and aerospace.
Case 1: Noise Simulation of Fresh Air Cabinets
The fresh air cabinet is a professional cabinet equipped with a fresh air system. It adopts the most efficient energy-saving technology - fresh air technology - to transfer heat out of the cabinet. It has the advantages of being dust-proof, purifying the air, being intelligent, and requiring no maintenance. It can completely replace the use of air conditioners and heat exchangers, and the temperature difference between the inside and outside of the cabinet can be controlled below 3 °C.
From the upper part of the cabinet, it can be seen that due to the influence of the structure, a velocity gradient (velocity difference) is formed. Judging from the colors, the velocity gradient has a difference of 4 - 8 m/s, so the velocity difference near the structure is quite large. This will be an important area where noise is generated. Near the fan, in addition to the air being directly drawn out by the fan, causing the traction of the stationary air flow beside it, the part where air is sucked in the circular cavity also forms a velocity gradient (velocity difference). Meanwhile, the vertically turning air flow is also a main reason for generating noise. As for the air structure at the lower part of the cabinet, it can be seen that the influence of the wind speed is rather chaotic (including the magnitude and angle of the speed). The velocity gradient (velocity difference) is relatively small, and the particle vibration noise will be smaller than that at the upper part. However, the cavity effect (like the sound of a drum) may be relatively large.
Preliminary judgment: Vorticity can reflect the distribution of sound to a certain extent. The red area represents the part with larger vorticity, and the blue area represents the part with smaller vorticity. It can be clearly seen that the vorticity is relatively large at the boundaries, especially near the boundaries where there are corners or other non-smooth transitions. At low speeds, vorticity will not form in non-boundary areas, and inside, it is only the propagation and attenuation of vorticity.
Case 2: Pneumatic Noise Analysis of Fans and Blowers
Pneumatic Noise Analysis of Fans:
Use the finite element simulation software (https://www.cae8.com) to simulate and calculate the flow characteristics and noise characteristics of fans / blowers. Fans can be used in many scenarios such as engine cooling. Reasonable fan design will greatly improve the efficiency of fans. However, due to the very complex internal flow of duct fans, it is very difficult to conduct qualitative analysis on their flow through theoretical calculations. Although wind tunnel tests can obtain their flow parameters and noise characteristics, they cannot describe the flow details inside the flow field. Therefore, simulation calculation is an effective design calculation method.
For the pneumatic noise analysis of fans, in Fluent, the simulation of blower noise is completed in two parts successively. First, the large eddy simulation model (LES) is used to solve the transient control equations in the fan flow field to obtain the dynamic stable value of the flow field, and the noise source of the fan (that is, the dynamic load on the fan blades) is obtained through the calculation results. Secondly, the method of solving the FW-H model is used to analyze the blower load and obtain the noise value.
Pneumatic Noise Simulation Analysis of Blowers:
Noise at specific fundamental frequencies and harmonic frequencies caused by the periodic rotation of blades; - Broadband noise: Broadband noise generated by turbulence, without very obvious fluctuations in the entire frequency range. The inlet velocities are set to 3 m/s and 12 m/s respectively, and the blower rotation speed is 24 rpm.
When setting up the simulation, first select the pressure-based steady solver, and choose the SST k-w model as the turbulence model. Set the inlet velocities to 3 m/s and 12 m/s, set the outer wall surface as the sym boundary, set the number of iterations to 2000 and start the calculation. After the calculation converges, change it to the transient state, use the sst k-w model, set the time step to 0.0001 s, and conduct a total of 50 steps of transient calculation until the result converges.
After the transient calculation of the pneumatic noise simulation is completed, activate the FWH pneumatic noise model, set the noise source as the blower, set a total of three receiving positions, and obtain the residual plot of the calculation process.
Conclusion: The sound pressure values of the blower are not large. As the incoming wind speed increases, the sound pressure values at the monitoring points increase significantly.
Case 3: Noise Calculation of Converter Cabinets
Both the inlet and outlet of the model are filter structures, and the inlet is composed of two layers of filters. Simulation calculation needs to be based on the porous media model. Plate heat exchange fins and disc-shaped reactors are placed in the left and right flow channels respectively, which need to be further simplified. - The wall surface contains a large number of pores, and the internal model flow channels are very complex. Simplification is carried out based on the operation process of the converter cabinet.
Average velocity distribution near the wall surface - The velocity gradient near the inlet of the fan is obvious, and the maximum velocity is about 30 m/s. - The velocities on the outlet wall surface are all below 20 m/s. In the middle of the model, due to the existence of the internal frequency converter, the air circulation area is very small, and the velocity on the wall surface is relatively high. - The low-velocity areas on the inlet and outlet wall surfaces are also very small, so it is necessary to reasonably arrange the wall sound-absorbing materials.
Comparison between the simulation at the center point 0.4 m at the bottom of the flow cabinet and the test data, and analysis of the sound-absorbing materials in the cabinet - After adding sound-absorbing materials, the noise peak at the main frequency (300 Hz) is reduced from 82 to 74.3, approximately a decrease of 7 - 8 dBA. - In the frequency band of 400 - 1000 Hz, the sound-absorbing materials can reduce the noise by about 20 dBA, as shown in the green line area in the figure, which also verifies the effect of the sound-absorbing materials on high-frequency sound absorption. - When no sound-absorbing materials are added, the curve has a maximum value around 250 Hz, which is related to the cavity mode. The 10th and 11th order cavity modes just correspond to around 250 Hz. It can be seen that the sound-absorbing materials can also eliminate excessive noise peaks.
The above are cases related to pneumatic noise simulation calculations.
Declaration: This article is originally created by Letu Zhizao official website. Please indicate the source when reprinting.
View more cases: Heat Dissipation Analysis Thermal Simulation Analysis Die Casting Mold Flow Analysis Modal Analysis CFD Analysis Electromagnetic Field Simulation Analysis Drop Analysis
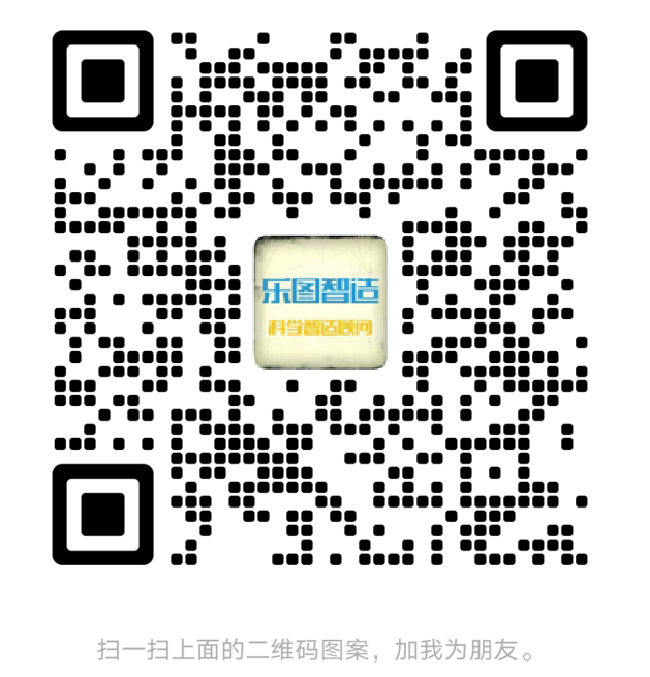
Leto Intelligent Manufacturing Technology (Suzhou) Co., LTD
199 4191 2022
Business consulting/technical consulting/exchange advice
Scan code wechat consultation, 24 hours to look forward to your voice