magma die-casting mold flow analysis flow channel simulation, cavitation erosion optimization
Business Content:
Genuine Flow3D, genuine magma die casting mold flow analysis (aluminum magnesium zinc copper), casting defect optimization, casting software sales, 1586 2324 033
Application value of die casting flow analysis:
Improve casting yield, greatly reduce the cost, shorten the development cycle. Through magma mold flow analysis to verify the rationality of the pouring system, as well as the rationality of product structure design, greatly reduce the porosity, shrinkage hole, cold insulation and other die casting defects, for you to improve the quality of castings, reduce manufacturing costs, numerical manufacturing technology magma mold flow analysis to enhance your company's market competitiveness. The era of numerical manufacturing technology guiding manufacturing is unstoppable. Authentic magma soft mold flow analysis results are accurate and reliable, with the latest solution algorithms, the latest material library properties, and comprehensive results output.
Note: Use MagmasofTV version 4.4 with caution, as it was released in Germany in 1988. The technology from decades ago, the solver is relatively old, the material database has not been updated for decades, and the accuracy is unmatched by the latest version.
Heat dissipation analysis of new energy vehicle battery pack coolant (Figure 1)
Successful cases:
Die casting mold Flow Analysis Case 1- Optimizing cavitation defects (optimizing flow path size and Angle) :
1. Part background:
The casting is an automotive gearbox housing of a large four-wheel drive truck. Aallied Die Casting of Rutherfordton, North Carolina (a division of RCM Industries),
2. Casting entrainment defect:
Casting local gas marks, porosity defects, scrap rate has reached more than 7%, which led to customers to require 100% of the casting leakage test; The castings that fail the leakage test should be impregnated. Due to the large volume of castings, there is an urgent need to provide a solution to reduce the cost loss caused by unforeseen defects. To provide customers with higher quality products.
3.magma die-casting mold flow analysis results (original mold scheme) :
magma mode flow analysis
FIG. 1: magma simulation results of the original mold show that there is an obvious enveloping flow phenomenon during the filling process, and too much air is trapped in the mold cavity, forming porosity defects. The result is consistent with the actual sample.
4. Cavitation improvement measures: (optimize mold plan) :
The gating system and runner design were optimized to reduce ensnaring and achieve a more balanced flow front. By making minor improvements to the pouring system and runner, and adjusting the Angle of the gate, the team succeeded in reducing ensnaring,
magma discusses magma mode flow analysis
The optimized runner design greatly reduced the incidence of air entrain, and after studying the air pressure results, they noticed that the design of the handed mold had insufficient exhaust. The optimized gating system has a more balanced flow front and improved air pressure.
Flow channel simulation for die casting analysis by magma (Figure 5)
After the implementation of these improved designs, casting quality has been greatly improved. Customers can cancel 100% leakage test and infiltration treatment. This saves customers time and costs, and the end result is that the elimination rate of products delivered to customers in the last six months is only 0.015% (157 ppm), which means that only about 21 products out of 130,000 castings are defective. Considering that the casting itself was a large machine part, the customer considered this a remarkable achievement. Aallied no longer requires secondary processing, no reprocessing, no 100 percent X-ray testing, and no 100 percent leak testing. Figure 3 shows a schematic diagram of a machined casting.
Die casting flow Analysis Case 2- Casting cavity balance optimization: (Optimize flow channel balance)
magma optimizes the flow channels
Saved about 12,000 euros, left: original pouring system, poor balance, inconsistent casting quality, low yield, right: optimized layout pouring system, balanced holes, consistent casting quality, improved yield,
Die casting mold Flow Analysis Case 3- Erosion Defect Optimization: (Optimize gate shape)
magma optimizes gate speed
Savings of around €25,000. Left: the original pouring system, gate speed is too high, mold erosion is serious, right: optimize the layout of the pouring system, reduce the speed of the inner gate, enhance the service life of the mold,
Die casting flow analysis Case 4 -- Development of complex and oversized die casting solutions:
1. Product background:
DGS Druckguss Systeme AG (Switzerland) in St.Gallen produces solar water heater panel frames. In order to better exploit solar energy, they have recently changed these frames from welded extruded parts to aluminum die castings. The main reason for changing the production process route is that die casting parts have a longer life and are more robust than welding parts. Since the roof assembly frame is subject to large temperature changes, this can lead to cracks in the welds of the welded frame. As a result, moisture penetrates the frame and damages the absorbing layer. Ultimately, this results in a huge loss of energy efficiency. However, die-cast frames have no such shortcomings and are therefore more robust. At the same time, the frame must fully meet the highest requirements: guaranteed corrosion resistance for at least 20 years, high dimensional accuracy and stability, low weight and lowest manufacturing costs. With a size of 2,050 x 1,230 x 50 mm and a weight of just 6 kg, the production was a huge challenge.
Oversized die casting
Above is the solar water heater panel frame: frame dimensions and section
2. Initial design simulation - warping deformation results:
magma deformation results
Analysis of warping deformation by magma shows that the deformation of the initial design scheme is very large (note: the display ratio is enlarged by 20 times; Left: vertical, right: horizontal)
3. Simulation of final design scheme:
DGS is well balanced. Axel Schmidt: "With MAGMA5, we have successfully produced this framework product from the very beginning in accordance with the strict requirements of time and cost. No process changes are required in production. Today, although the weight of the die-cast liquid metal is 24 kg, the weight of the obtained parts is only 6.3 kg, the filling time is only 40 milliseconds, and we produce the frame without major deformation. This project is not only an economic success, but also the latest proof of DGS 'ability to innovate."
magma optimization deformation
Left: Final pouring system design simulation results: temperature distribution after filling. Right: casting sample
Other MAGMA die-casting mold flow analysis cases:
magma die Casting Flow Analysis Flow channel simulation (Figure 3)magma die casting Flow Analysis Flow channel simulation (Figure 2)
Core advantage:
1. Authentic flow3d/MAGMA model flow analysis software with accurate and reliable results, the latest solution algorithm, the latest material library properties, and comprehensive result output.
The era of numerical manufacturing technology guiding manufacturing is unstoppable. Through the mold flow analysis to verify the rationality of the mold design scheme, as well as the rationality of product structure design, greatly reduce the lack of material, trapped gas, shrinkage, cracking, deformation and other forming defects, for you to improve the quality of products, reduce manufacturing costs, numerical manufacturing technology to enhance the market competitiveness of your enterprise.
2. Opened for more than ten years, gold consultant led the team, rich experience in industry-university-research practice and application.
Familiar with SAIC, BAIC, GAC, Changan, GM, BMW, Tesla and other Oems with high precision and high requirements. To provide customers with not only the "mode flow analysis report", is able to guide the production of a powerful theoretical data basis.
3.CAD/CAE/CAM product chain is complete, providing you with one-stop collaborative development.
From the design and analysis of the product end to the design and analysis of the mold forming end, experts in various fields have a good connection to each link and consider each link globally.
4. 100,000 high-end server, efficient order completion, to meet the delivery needs of all levels.
In order to meet the increasingly rapid development cycle, the company is equipped with high-end hardware + experienced experts + the latest version of software solution software = efficient operation.
5. Charge honest and reasonable, customer demand-oriented, recommend the most suitable product plan for each customer.
Good products are naturally expensive, but not necessarily the most suitable, customer demand-oriented, for each customer to develop the most suitable product plan. Honesty, quality first, heart service, win trust.
Charge method:
Flow channel simulation for die casting analysis by magma (Figure 11)
Contact consulting, explore scientific casting solutions, and create higher added value together
Letu Intelligent Manufacturing Technology, product performance optimization, finite element analysis engineering services, software sales, provide scientific numerical information technology solutions,
Statement: This article is original from the official website of Le Tu wisdom, please indicate the source.
See more cases: Finite Element simulation Die casting mold flow Analysis Electromagnetic Field simulation analysis Drop analysis Fatigue analysis CFD analysis Casting deformation analysis
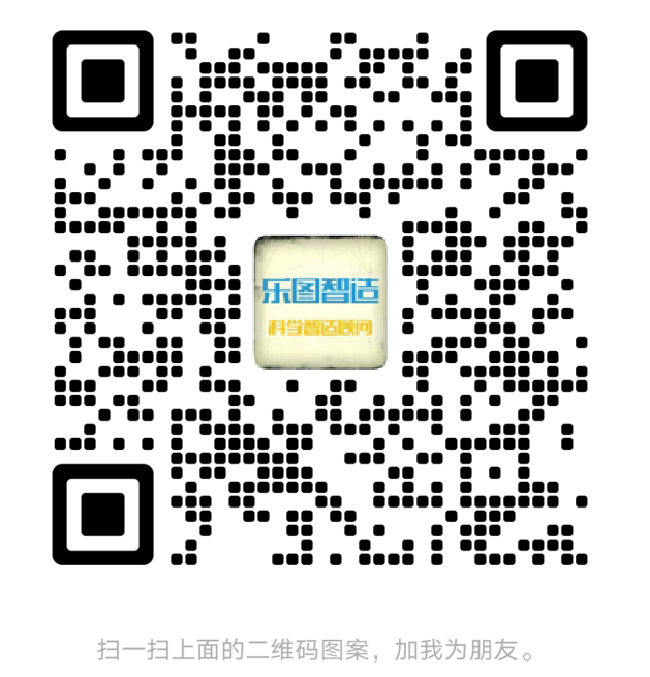
Leto Intelligent Manufacturing Technology (Suzhou) Co., LTD
199 4191 2022
Business consulting/technical consulting/exchange advice
Scan code wechat consultation, 24 hours to look forward to your voice