Gearbox shell magma low pressure casting simulation
Business Content:
The latest authentic Flow3D, authentic magma low-pressure casting simulation outsourcing, casting defect optimization, low-pressure casting solution development, casting simulation software sales, to provide scientific numerical information technology solutions for manufacturing enterprises.
Application value of casting simulation:
In the low pressure casting process of aluminum alloy castings, the main difficulty is the shrinkage problem of castings. The reliable Magma casting simulation software is an important scientific tool to solve the shrinkage problem, which can accurately predict the area and volume of shrinkage.
Application case
Gearbox shell low pressure casting simulation:
This is a gear cover aluminum alloy casting, gear box is an important transmission mechanism in the auxiliary power unit. It is connected to the auxiliary power unit, transmits shaft power from the internal wheel train, and provides mounting fulcrum for the motor, motor, oil pump, starter. As the main bearing part, the bearing capacity of the gearbox shell affects the working stability of the gearbox.
Gearbox shell magma Low pressure Casting Simulation simulation (Figure 1) Gearbox Shell magma low pressure casting simulation simulation (Figure 2)
Usually the strength requirements of gearbox shell castings:
As the main bearing part, the bearing capacity of the gearbox shell affects the working stability of the gearbox. Therefore, this has high requirements for the strength of the casting parts,
1. No porosity defects.
2. Can not have the problem of under-casting and filling,
3. Casting density requirements are high, can not have shrinkage problems.
Gearbox housing
Molding scheme evaluation:
According to the above requirements, in order to obtain better quality castings, the more commonly used low-pressure casting molding process is used.
Reasons for adopting magma's Low Pressure Casting simulation module:
1. High shrinkage risk, magma low pressure casting simulation shrinkage results are accurate and reliable,
Because the overall wall thickness of this product is relatively thick, there are still a large number of areas with large thickness drop, so the main difficulty of this product is the casting shrinkage problem, the reliable Magma casting simulation software is an important scientific tool to solve the shrinkage problem, it can accurately predict the easy shrinkage area and shrinkage volume size.
2.CAD/CAE/CAM integration technology is the development direction and trend of low pressure casting technology.
Low pressure casting process is more sensitive to filling and pressure holding parameters. Therefore, by studying the mathematical model of low pressure casting simulation and its solving conditions, two kinds of filling process parameters are adopted to simulate and optimize, so as to determine a reasonable filling process plan.
Low pressure casting simulation filling results:
Next, we take a look at the results of magma's low-pressure casting simulation analysis. The following is a video animation of the filling process, the filling effect is good, there is no problem of filling dissatisfaction, we can clearly see that the liquid from the riser slowly upward and smooth filling, liquid metal filling is stable, reduce or avoid the metal liquid in the filling of the churn, impact, splash phenomenon, thereby reducing the formation of oxidation slag, avoid or reduce casting defects, improve casting quality.
magma low pressure casting simulation filling results
Simulated solidification results of low pressure casting:
The picture below shows the overall solidification process of the casting. From the results, it can be found that there are some local isolated liquid phase, which is the risk area of late solidification and peripheral characteristics.
As we mentioned earlier, the overall wall thickness of this product is relatively thick, and there are still a large number of areas with large thickness drop. Therefore, the main difficulty of this product is the shrinkage and loosening of castings.
magma low pressure casting simulation solidification sequence results
Simulated porosity reduction results of low pressure casting:
Then, let's take a look at the more intuitive analysis results. The following figure is the result of the porosity of the shrinkage hole, and the blue in the circle represents the location of the shrinkage and porosity.
Casting simulated porosity results
magma simulated thermal node distribution results for low pressure casting
Conclusion:
It can be found from the above results that the comprehensive evaluation of other relevant results, such as: oxide skin, air pressure, temperature, etc., is omitted here. The comprehensive evaluation conclusion can be said that the overall casting effect is good, and the shrinkage and loosening risk still exists, mainly because the local wall thickness distribution of the product is too thick, and it is difficult to effectively fill in place.
The results of this analysis will serve as a useful theoretical basis for the manufacturer to discuss with the end customer the optimization of the local thickness distribution of the casting. Cooperate with product design scheme optimization to make further development scheme. It can also have a more powerful assessment basis for manufacturing risk assessment.
Advantages of low pressure casting process:
1. It has absolute advantages in eliminating stomata,
Because the low pressure casting process can ensure that the liquid metal filling is stable, reduce or avoid the billowing, impact, and splashing phenomenon of the metal liquid when filling the mold, thus reducing the formation of oxidation slag, avoiding or reducing the defects of the casting, and improving the quality of the casting.
2. Good for surface quality,
Liquid metal filling under the action of pressure, can improve the flow of liquid metal, casting formability is good, is conducive to the formation of clear outline, surface smooth casting, for the formation of large thin-wall castings more favorable.
3. Advantages for casting density,
The casting crystallizes and solidifies under the action of pressure, and can be fully supplemented, so the casting has dense structure and high mechanical properties.
Disadvantages of low pressure casting process:
1. The freedom of the gate scheme is small, thus limiting the product. (Gate location, quantity restrictions, product internal wall thickness changes, etc.)
2. Long casting cycle and poor productivity. In order to maintain directional solidification and liquid flow, mold temperature is high and solidification speed is slow.
3. The structure near the gate is thick, and the mechanical properties of the lower surface are not high. 4) Comprehensive and strict management (temperature, pressure, etc.) is required
Charge method:
Flow channel simulation for die casting analysis by magma (Figure 11)
Contact consulting, explore scientific casting solutions, and create higher added value together
Letu Intelligent Manufacturing Technology, product performance optimization, finite element analysis engineering services, software sales, provide scientific numerical information technology solutions,
Statement: This article is original from the official website of Le Tu wisdom, please indicate the source.
See more cases: Die casting mold Flow Analysis Finite Element Simulation Electromagnetic Field simulation MAGMA Analysis Simulation Drop analysis Fatigue analysis CFD analysis Casting deformation analysis Casting simulation
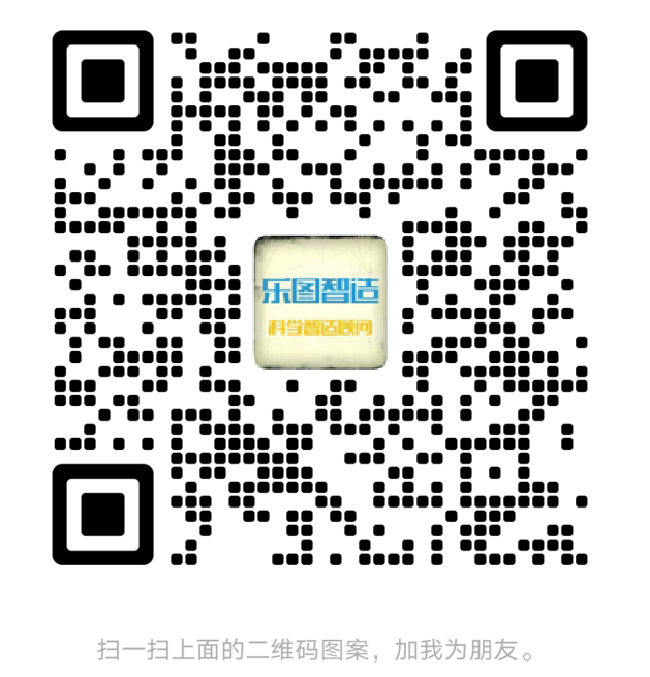
Leto Intelligent Manufacturing Technology (Suzhou) Co., LTD
199 4191 2022
Business consulting/technical consulting/exchange advice
Scan code wechat consultation, 24 hours to look forward to your voice