Electrothermal coupling welding simulation
Business Scope:
Undertake all kinds of welding simulation outsourcing, software sales, and finite element analysis simulation solutions..
The Main Significance of Welding Simulation
1. Optimize the welding process. Through finite element analysis technology, the distribution of temperature field and stress field in the welding process can be predicted, so as to optimize the welding process, improve the quality of welds and reduce the degree of deformation.
2. Reduce the test cost. The traditional welding process design requires a large number of tests to determine the best scheme, which is not only time-consuming but also costly. Through numerical simulation technology, simulation experiments can be carried out on the computer, avoiding the waste of test costs.
What Are the Analysis Results of Welding Simulation?
The development of welding numerical simulation technology has gradually started with the accumulation of welding practical experience and the development of finite element analysis simulation technology, computer technology, etc. The simulation of the welding process mainly focuses on several aspects such as welding temperature field, welding residual stress, welding deformation, aiming to improve the manufacturing quality of welded components, enhance the service performance of products, and optimize the welding sequence and other technological processes. The quality of traditional welding relies heavily on the experience of welders, while welding numerical simulation technology uses numerical simulation methods to find optimized welding process parameters, such as welding materials, temperature control conditions, fixture conditions, and welding sequence.
Welding Simulation - Residual Stress Distribution Results
It can be seen that the longitudinal stress and the transverse stress show the same stress distribution trend on the welding line, but the stress values are different. And along the middle area of the welding line, there is a trend of gradually increasing stress. Although the flat plate is completely symmetrical, the stress distribution here is not symmetrical. This is mainly because the overall temperature of the welded parts gradually increases during the welding process, resulting in a gradually increasing trend of the final residual stress.
After welding, the flat plate has warped deformation, and the maximum residual stress generated by welding is located in the weld area, approximately 440 MPa.
Welding Simulation - Temperature Field Analysis
Electro-thermal coupling analysis, heat generated by resistance, dielectric and magnetic losses in high-frequency state. The temperature field is an important part of the welding process.
Welding Simulation - Welding Pool Morphology
The morphology of the welding pool along the thickness direction of the plate. Due to the too fast welding speed, the plate is not fully penetrated during the welding process, and the welding pool presents a flat shape instead of a spherical shape.
Welding Simulation - Equivalent Plastic Strain (PEEQ) Distribution Results
It can be seen from the figure that the deformation value in the right area is 0, while in the left area, as the temperature gradually drops below the melting point, plastic strain values begin to accumulate. Taking the welding simulation of vehicles as an example, more attention is often paid to deformation than to stress. This does not mean that stress analysis is not important, but the perspectives are different. The stress of welding has been judged for the safety of the process through other means (it is actually difficult to accurately calculate the stress of large components in welding simulation). However, welding deformation has a significant impact on the subsequent installation.
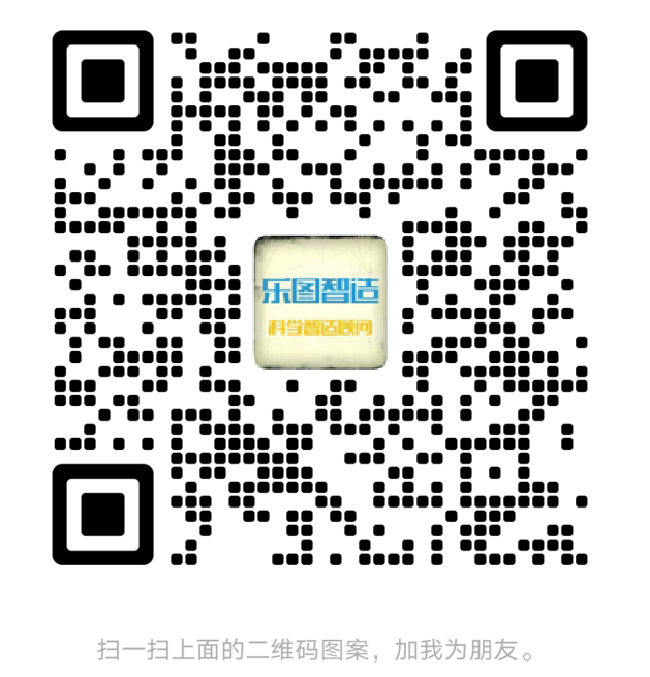
Leto Intelligent Manufacturing Technology (Suzhou) Co., LTD
199 4191 2022
Business consulting/technical consulting/exchange advice
Scan code wechat consultation, 24 hours to look forward to your voice