What is the value of lightweight design, and what are the ways of lightweight
The prices of raw materials have skyrocketed, and the market competition is fierce. Lightweight engineering can give you a helping hand. Letu provides scientific manufacturing solutions for manufacturing enterprises.
Value of Lightweight Finite Element Analysis:
1. Reduce weight to save material costs, lower construction costs, and increase profit margins.
2. Save resources, reduce energy consumption and environmental pollution.
3. Achieve sustainable development.
The above three points have become two major problems to be solved in the global automotive industry. According to statistics, for every 10% reduction in vehicle weight, fuel consumption can be reduced by 6% - 8%. Therefore, reducing vehicle weight is one of the most basic ways to save energy and improve fuel economy. Vehicle lightweighting is becoming the frontier and hot topic of automotive technology in the 21st century.
There are two main ways for lightweighting:
1. Use CAD/CAE numerical technology to optimize the designed structure, reduce weight while taking into account the requirements of structural strength. Make parts thinner, hollow, smaller, composite, and improve the structure and process of parts to minimize the mass of parts to the greatest extent. These two approaches complement each other. Only by combining material replacement with structural improvement can the mass of each part be minimized on the premise that the overall quality and performance of the vehicle are not affected. Using CAE finite element analysis technology to achieve vehicle lightweighting has incomparable advantages over traditional design methods.
2. Adopt lightweight materials, such as new materials with higher strength and lighter weight like aluminum alloys and high-strength steel.
Taking the automotive manufacturing industry as an example:
Research Objects of Vehicle Lightweighting:
From the overall structure of the vehicle, parts that account for a large proportion of the total vehicle mass include the body, engine, chassis, internal and external equipment, etc. Therefore, the lightweight research on parts such as the body, chassis, and engine has great potential for reducing the total vehicle mass.
Introduction to Lightweight Application Cases:
1. Existing products of the body in white
2. Lightweight coefficient of the body in white
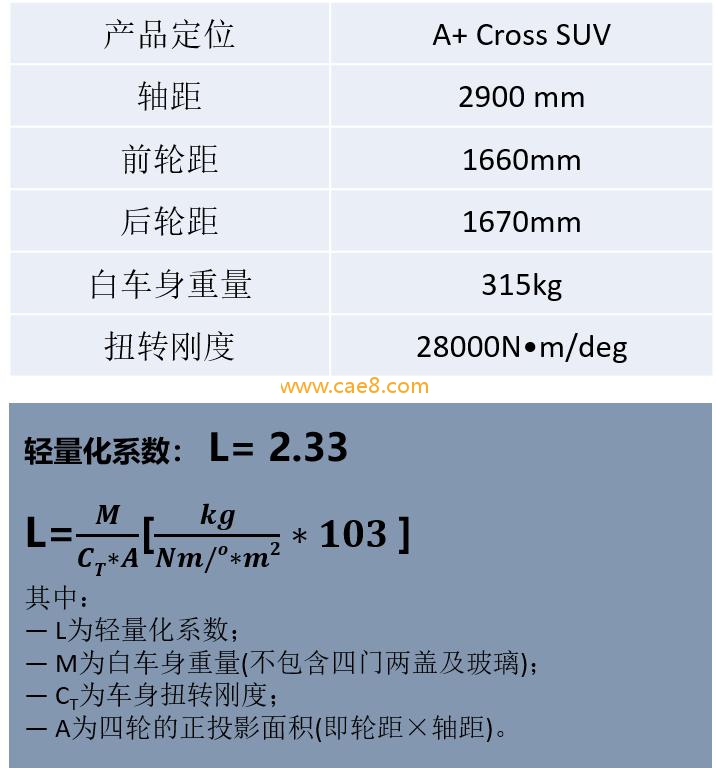
3. Material distribution of the body in white
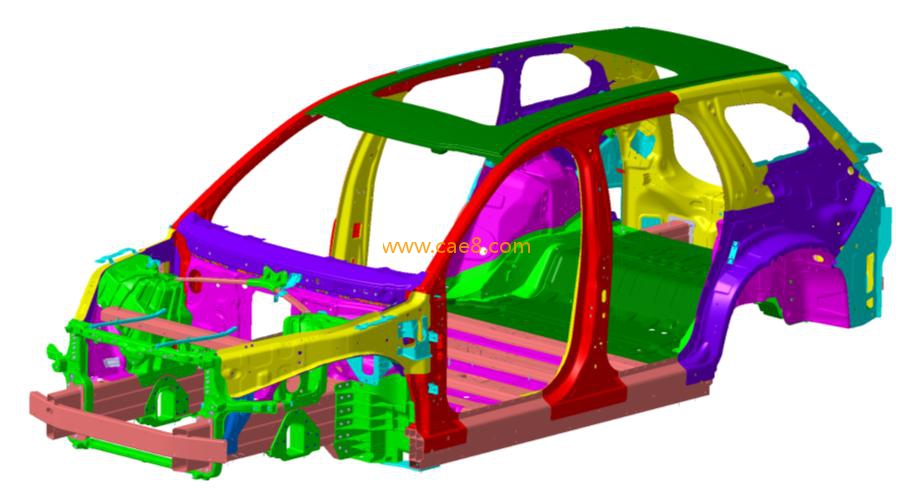
In lightweighting engineering, adoptnew materials and new forming process technologies
01. Aluminum alloy casting process forming. Aluminum alloy castings adopt the most advanced CAE topological simulation method:
The structure is simplified, and the weight is reduced by 15%;
The stiffness is improved, and the body stiffness is increased by 18%;
The collision performance is optimized, and the collision performance is improved by 8%;
02. Aluminum alloy extrusion process forming. Aluminum alloy extrusions adopt the most advanced CAE topological simulation method:
The structure is simplified, and the weight is reduced by 20%;
The stiffness is improved, and the body stiffness is increased by 15%;
The collision performance is optimized, and the collision performance is improved by 12%;
03. TRB hot forming technology, high-strength unequal-thickness material hot forming technology for B-pillars:
Unequal thickness, with a 10% weight reduction;
Strength improvement, with a 60% increase in yield strength;
Side impact optimization, with a 30% improvement in side impact performance;
Good formability, enabling deep drawing;
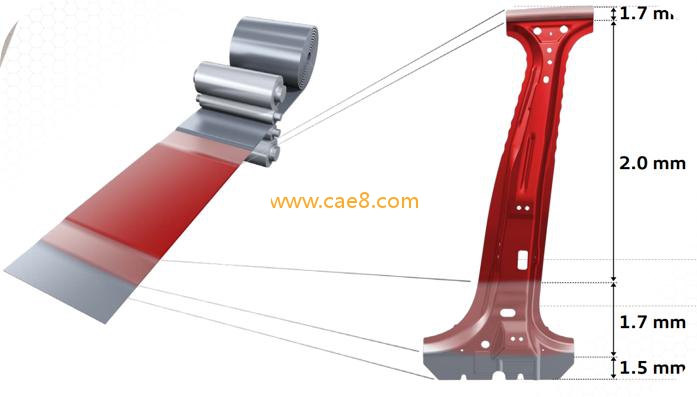
04. Carbon fiber. The roof reinforcement panel and rear floor are formed by high-strength and high-modulus carbon fiber molding technology:
Low density, with a 30% weight reduction compared to aluminum alloys;
Stiffness improvement, with a 20% increase in body torsional stiffness;
Durability improvement, with an 18% increase in body durability performance;
Collision performance improvement, with a 12% improvement in side impact performance;
In lightweighting engineering, adopt new assemblyprocess technologies
01. Joining process - SPR
Under the action of external force, SPR rivets penetrate the first layer of material and the intermediate layer of material, and flow and extend in the bottom layer of material to form a permanent plastic deformation that is interlocked with each other. Such a rivet joining technology is called self-piercing riveting:
It is suitable for double-layer and multi-layer joining of the same and different materials;
It belongs to mechanical cold forming joining without heat input, avoiding the problem of thermal deformation; The static strength and fatigue strength are higher than those of spot welding joints;
The joining quality can be controlled during the process, and the quality is reliable;
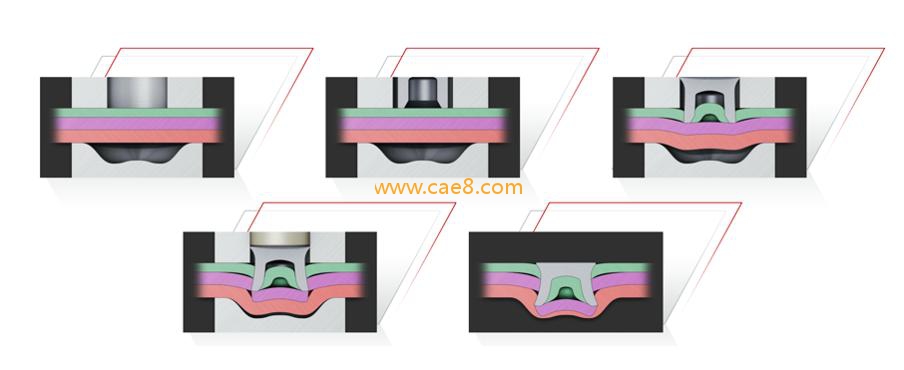
02. Joining process - FDS
The FDS flow drilling screw tightening process is a cold forming process in which the high-speed rotation of the motor is transmitted to the plate to be connected through the tightening shaft in the center of the equipment, generating heat by friction to produce plastic deformation, and then self-tapping and screwing:
It is suitable for double-layer and multi-layer joining of the same and different materials;
The screws are detachable, which is convenient for maintenance;
It can be operated on one side and has a wide range of applications;
The joining quality can be controlled during the process, and the quality is reliable;
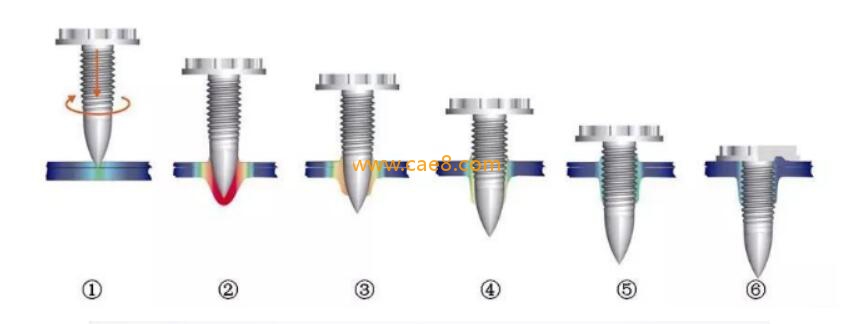
03. Joining process - CMT
Cold metal transfer (CMT) is a new welding process technology without slag spatter:
It reduces the welding deformation of thin plates and enables the weld to have a good bridging ability at the same time;
The arc remains stable all the time, and there is almost no spatter during the welding process, and even no burn-through phenomenon;
It can be operated on one side and has a wide range of applications;
It can realize the connection between steel and aluminum.
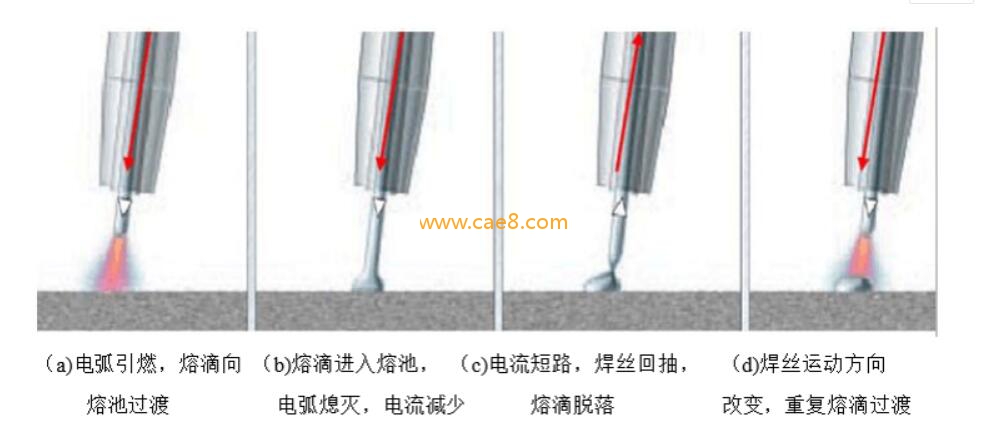
Finite Element Analysis Cases:
Analysis of Heat Dissipation of Battery Packs Analysis of Die Casting Mold Flow Modal Analysis CFD Analysis Electromagnetic Field Simulation Analysis IC Chip Packaging Analysis Rubber/Silicone Mold Flow Analysis Gravity Casting Simulation Analysis Casting Deformation Analysis
Scan QR code and communicate with project manager
We look forward to your voice on wechat 24 hours
Business consulting/Technical consultation/ Technical consultation/ Technical consultation
Solemnly declare: the display is already listed old products, has been authorized to display, we strictly keep confidential information for customers.