Vehicle air outflow field cfd analysis/windage analysis
Business Contents:
CFD Analysis and Simulation, Drag Analysis, Flow Analysis, CFD Analysis of the External Air Flow Field of Automobiles, Providing Professional Finite Element Analysis Consulting for Manufacturing Enterprises, with Rich Project Experience and Knowledge Accumulation in Fields Such as New Energy Vehicles, High-tech, Medical Care, and Industrial Equipment.
Application Value of CFD Analysis:
Problems such as vehicle instability at high speeds and deviation in crosswinds are closely related to the aerodynamics of vehicles. By optimizing the aerodynamic design, relevant performances of vehicles, such as fuel consumption and driving safety at high speeds, can be effectively improved. Generally speaking, the better the streamline shape of a vehicle is, the better its aerodynamic performance will be.
Drag Analysis - Concept of Drag Coefficient:
For vehicle manufacturing by enterprises, there are more and more designs. In recent years, the term "drag coefficient" has come into everyone's view. However, people still haven't fully understood what's behind the drag coefficient. What exactly can the drag coefficient of a vehicle determine? Is it always better to have a lower drag coefficient for a vehicle?
In fact, the wind resistance of a vehicle is tested by placing the vehicle at the wind tunnel entrance. It belongs to the category of CFD simulation analysis. Wind tunnel tests can be said to be very important tests in many industries and can even affect a country's industrial level. Whether a skyscraper can stand firmly and withstand strong winds needs to be determined through wind tunnel tests. Even whether an aerospace vehicle can successfully reach outer space also requires strict wind tunnel tests.
Project Case of CFD Analysis of the External Flow Field of the Whole Vehicle
Drag analysis can achieve excellent aerodynamic performance. For this, a forward development approach should be adopted. The so-called forward development means getting involved early in the initial stage of product development and actively and flexibly conducting design in each development stage until the goals set for the vehicle are achieved. During the detailed design stage of product development, engineers conducted analysis on more than 100 optimization schemes based on simulation technology, not missing any design details. Eventually, the drag coefficient was as low as 0.34.
Air Flow on the Front Windshield Drag Analysis Situation
The front windshield and the hood are the main areas where wind resistance is generated. To improve the aerodynamic design of this part, engineers conducted 23 rounds of CFD analysis and verification, optimized the angle of the front face, made the front windshield tilt backward, allowing air to pass through the front of the vehicle more easily. While effectively reducing air resistance, good driving vision was also taken into account.
Analysis of the "Vortex Area" at the Rear and the Air Flow on the Side Drag Analysis Situation
1. When a vehicle is running, a "vortex area" will form at the rear. This is similar to the situation where an object is sucked into a vortex by a "tornado". The faster the air flow speed in the "vortex area" is, the stronger the backward suction force on the vehicle will be, and the greater the resistance will be. It is one of the important factors considered in drag analysis.
2. After 21 rounds of CFD analysis and simulation verification and wind tunnel verification of 4 schemes, the rear wing was designed with an optimal downward angle of 14°, which successfully and significantly reduced the air resistance at the rear of the vehicle and effectively avoided the formation of vortices on the rear wing.
3. To prevent high-speed air flow from rushing into the "vortex area" at the rear, based on the data obtained from wind tunnel tests, the optimal design scheme for the side rear wing - a blade-shaped design - was also generated. This not only effectively reduces the size of the trailing vortex but also cuts the air flow and reduces the intensity of the "vortex".
Analysis of the Air Flow on the Chassis Drag Analysis Situation
To reduce the air resistance generated by the vehicle chassis, engineers usually adopt a chassis flattening design, that is, arranging the chassis components on a plane as much as possible and achieving flattening by installing protective plates. There are a total of 11 chassis flattening protective plates, which can effectively improve the air flow under the vehicle, enhance smoothness, allow air to quickly pass through the bottom of the vehicle body, reduce air resistance by 6% and air lift by 50%. The drag analysis control is very good.
CFD Analysis Wind Tunnel Air Flow Circulation System
The advantage of a wind tunnel is that it can generate air flow that is very close to the actual driving situation. If equipped with a turntable, the vehicle can be tested at different wind incidence angles. This device is a typical wind tunnel. Besides placing the wind generating device (fan, silencer and air heater) above the measurement chamber, the vehicle to be inspected is placed on the turntable and rotated 90° towards the exhaust nozzle valve. The typical wind speed used by the system is about 140 km / h (with a maximum of 160 km / h).
CFD Analysis Wind Noise Control
High-quality quietness is a basic requirement for products. To control wind noise at high speeds, engineers have carried out multiple rounds of optimization through CFD analysis and simulation, wind tunnel tests, etc., continuously improving the aerodynamic noise sources. Eventually, the interior noise of the vehicle at a speed of 120 km/h was optimized to 65.2 decibels, which is significantly better than that of joint-venture vehicles of the same level.
The automobile industry is one of the most important industries in the world at present and also one of the most competitive industries. In the modern vehicle design process, CAE analysis plays a very important role. The highly competitive vehicle market has put forward high requirements for the development cycle and quality performance of vehicles. The role of CAE lies in that it can drive lean design and a rapid vehicle development process, which can greatly save development costs and shorten the development cycle.
Commonly Used Test Items for CFD Analysis in the Vehicle Industry
Drag analysis and aerodynamic noise analysis
CFD simulation analysis of the external flow field of the whole vehicle
CFD analysis of the air conditioning system
Analysis of the whole vehicle thermal management
Analysis of the whole vehicle aerodynamic noise
Contact Us for Consultation, Explore Scientific Manufacturing Solutions and Create Higher Added Value Together
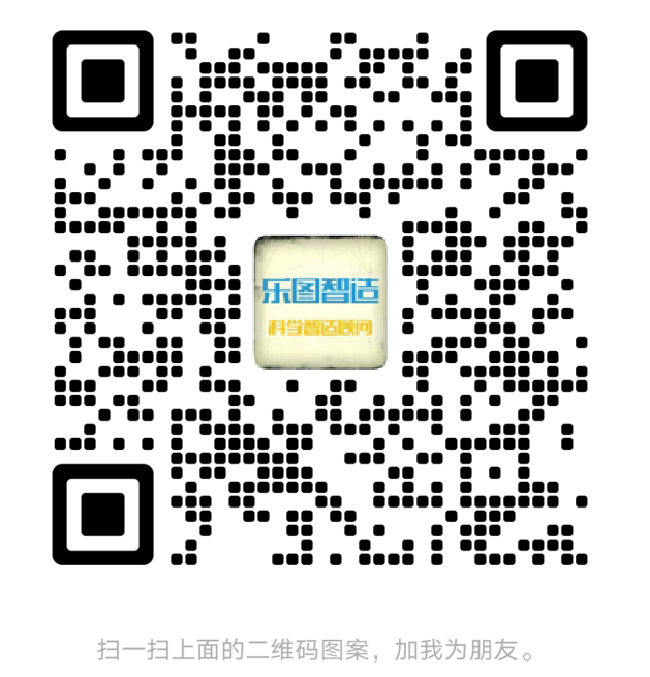
Leto Intelligent Manufacturing Technology (Suzhou) Co., LTD
199 4191 2022
Business consulting/technical consulting/exchange advice
Scan code wechat consultation, 24 hours to look forward to your voice