magma Software has announced the release of version 5.5 of its casting simulation software Magmasof
Important Announcement: In 2021, the magma software company grandly released the MAGMASOFT 5.5 version, adding sand core deformation results, updating and adding more functions, and making the solution algorithm more accurate.
The MAGMASOFT 5.5 of the magma software company has made many improvements in usability, bringing you a simpler and more efficient user experience and making the accuracy more reliable.
With efficient casting development, reliable start of production, and a robust process window, numerous new options in version 5.5 help you create more value in casting design, mold manufacturing, and casting production. We have also made further improvements to the software to bring you a simpler and more efficient user experience.
The magma software company has improved the functions of the cast iron module
Cast iron foundries can use the brand-new functions to measure the impact of metallurgy and metal treatment on solidification and feeding behavior. With the innovative SMAFEE feeding algorithm, you can better understand the impact of melt quality, inoculation effect, and local pressure distribution on shrinkage cavities. In addition, thermal convection during the solidification process is now a standard option for cast iron. Thermal convection affects the temperature distribution and thus the feeding behavior of large castings and mass-produced parts. The new feeding model is applicable to all types of cast iron: ductile iron, gray iron, and compacted graphite iron.
The magma software company has added quality assessment in die casting
In high-pressure die casting, entrapped gas and shrinkage cavity defects are the main causes of waste products. Therefore, mold and process designs focus a lot on reducing pores caused by entrapped gas. Using MAGMASOFT® 5.5 can reliably predict the mass balance of air in the cavity and the movement of the entrapped gas. In the new "Gas" result, you can see the quantitative results of the gas in the cavity and in the molten liquid and conduct a comprehensive assessment throughout the filling process. During the entire development process of the project, even under changing process conditions, the quality of the mold design and process conditions can be continuously evaluated.
Added the deformation of sand cores during the casting process
The MAGMASOFT 5.5 launched by the magma software company can predict the stress and deformation of sand cores during the filling and solidification processes, preventing casting defects caused by sand core deformation or failure. We can provide a large amount of material data for various sand/binder combinations. In addition to cold cores, we also pay special attention to predicting the deformation modes of inorganic sand cores. These unique functions avoid core breakage, can predict local dimensional deviations, and achieve pre-compensation for sand core deformation by improving the core box design, providing users with higher security.
The above figure shows the sand core deformation data of the motor housing during the filling process.
Optimization of heat treatment for steel castings
MAGMASOFT® has long had the function of calculating heat treatment. You can check whether the set heat treatment process conditions can meet the customer's requirements for the metallographic structure and mechanical properties of the castings. Now, the software has broadened the applicable range of alloy compositions, including low-alloy and high-alloy steel grades. The prediction of the metallographic structure and mechanical properties after heat treatment takes into account the growth of austenite grains and provides a new result of the cooling rate in the critical temperature region during the quenching process. A unique function of the new version is that the calculated composition information of the local segregation of the casting is transferred from the casting process to the heat treatment simulation.
MAGMA CC - Now Available for Continuous Casting of Steel
The new version of MAGMA CC launched by the magma software company can be more effectively applied to all continuous casting processes, simulating the continuous casting of steel for all typical specifications and machines (including curved continuous casting machines). In the new 5.5 version, many enhanced functions can be used for the simulation of the startup process and the thermal and mechanical aspects of the entire casting stream. In addition, the formation of center cracks can also be evaluated.
MAGMASOFT® Helps You Achieve Your Goals Faster
The use of the software should simply and effectively support the daily work of users, and the time to solve problems must be as short as possible. This is exactly our goal: MAGMASOFT® 5.5 has made many improvements in usability to help you obtain the required results faster. The MAGMAinteract® launched by the magma software company can promote communication and exchanges between suppliers and customers as well as all companies and employees interested in the results of MAGMASOFT®. MAGMASOFT® 5.5 provides new potentials for users and decision-makers in many different fields, ensuring and improving the efficiency of casting design, mold design, and production processes. Let numerical technology drive scientific intelligent manufacturing.
Contact us for consultation, explore scientific casting solutions, and create higher added value together
Disclaimer: This article is sourced from the official website of the magma company. Suzhou Letu will match the best casting software for you.
View more cases: Lightweight Design Battery Pack Heat Dissipation Analysis CFD Analysis Casting Shrinkage Porosity Analysis Die Casting Mold Flow Analysis Casting Deformation Analysis Casting Simulation
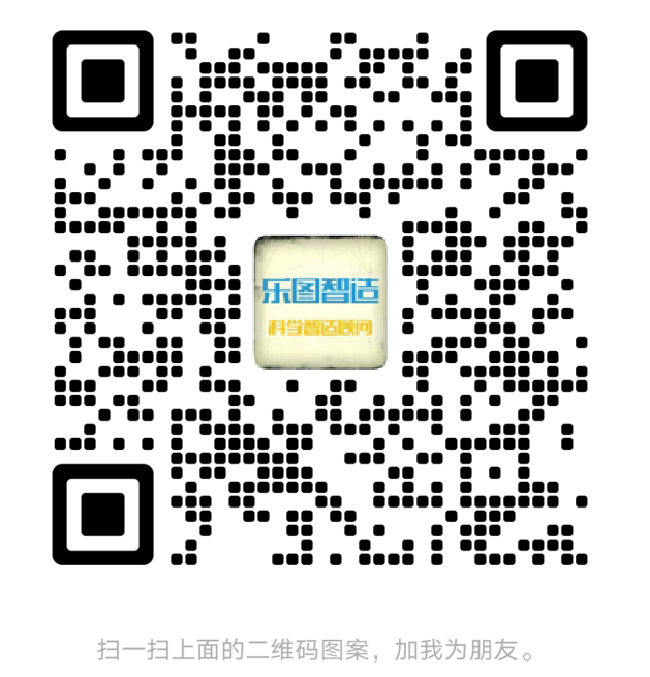
Leto Intelligent Manufacturing Technology (Suzhou) Co., LTD
199 4191 2022
Business consulting/technical consulting/exchange advice
Scan code wechat consultation, 24 hours to look forward to your voice