Fei Heng - Finite Element Simulation Consultant
Letu Intelligent Manufacturing Technology (Suzhou) Co., Ltd
Finite element simulation consultant Fei Heng
Current age: 31 years old
Education: Master of Solid Mechanics
Industry experience: 6 years
Previously worked as a senior finite element simulation engineer in a company
Specializes in:
1. Simulation of strength, fatigue, drop, impact, vibration noise, and other directions.
3. Secondary development of simulation software scripts, completing customized secondary development of the entire process from simulation modeling to result analysis and output reports.
3. With a solid foundation in mechanics theory, proficient in secondary development at the solver level.
Project experience:
Simulation of New Energy Vehicle Connector and Charging Gun Project:
Project 1: Comparison of Strength and Stiffness of Three Charging Gun Heads - Compression Simulation Simulating Human Pulling Damage
Project 2: Analysis of Insertion and Insertion Force/Insertion Stress Diagram/Insertion Life of Rotary Spring Terminal
Project 3: Force analysis of low tooth difference motion, transmission speed analysis, strength simulation of gears during low-speed operation, and strength analysis of tooth roots during locked rotor and high-speed operation of helical gears and face gears.
Project 4: Analysis of Charging Gun/High Voltage Connector Insertion
Project 5: Strength Analysis of High Voltage Connector/Charging Stand End Cover Buckle
Project 6: Experimental analysis of collision level of charging pile IK10 (ball drop analysis)
Project 7: Modal analysis and random vibration analysis of charging machine (using engine load power spectrum)
Project 8: Steady state/transient analysis of temperature rise when the rotating spring/busbar is energized
Project 9: Analysis of Thermoplastic Forming of High Voltage Connectors. (Model flow analysis)
Project 10: Analysis of busbar inductance. (Inherent attribute)
Project Eleven; Analysis of rebound force and rebound amount of shielding film.
Project 12: Using Helios software, import the melt line and fiberglass layout results from Moldflow flow analysis into Abaqus structural simulation, view the product strength at the melt line position, and evaluate the risk issues of gear operation considering injection molding.
New Energy Battery Pack Project:
Complete the physical modeling, simulation environment construction, structural stress analysis, fluid analysis, heat transfer analysis, thermal coupling, etc. of lithium battery equipment automation production line equipment. Simulation includes but is not limited to the following types: automatic winding strength and displacement accuracy simulation, temperature field simulation optimization and flow field simulation evaluation of battery pole plate oven, simulation optimization of static pressure chamber wind speed uniformity, strength simulation of slurry mixing equipment, simulation of heat transfer effect of heat exchanger, simulation optimization of rolling roller displacement accuracy, simulation analysis of transient temperature of water-cooled roller, etc.
Chuanqi SUV project
1. Grid division and its quality inspection.
2. Using CAE software for welding automotive components.
3. CFD analysis: air duct flow and vehicle outflow field, defrosting and defogging.
4. Write an analysis report based on the analysis results (including improvement suggestions, etc.).
5. Cooperate with design engineers to solve design problems that arise in practice.
6. Lead the completion of CAE vehicle analysis tasks and allocate work tasks.
Lifan GC01
1. Grid division and its quality inspection.
2. Using CAE software for welding automotive components.
3. Perform modal, strength, stiffness, and other analyses on the entire vehicle and its components.
4. Write an analysis report based on the analysis results (including improvement suggestions, etc.).
5. Cooperate with design engineers to solve design problems that arise in practice.
BAIC Yinxiang VA01
1. Grid division and its quality inspection.
2. Using CAE software for welding automotive components.
3. Perform modal, strength, stiffness, collision, CFD, and other analyses on the entire vehicle and its components.
4. Write an analysis report based on the analysis results (including improvement suggestions, etc.).
5. Cooperate with design engineers to solve design problems that arise in practice.
Dongfeng Xiaokang K01
1. CFD analysis of vehicle external flow field analysis, air duct internal flow analysis, etc
2. Analysis of vehicle collision, mode, stiffness, strength, etc
3. Based on the analysis results, write an analysis report and provide corresponding suggestions
Proficient in software:
Abaqus、Ansys、HyperWorks、Virtual.Lab
.
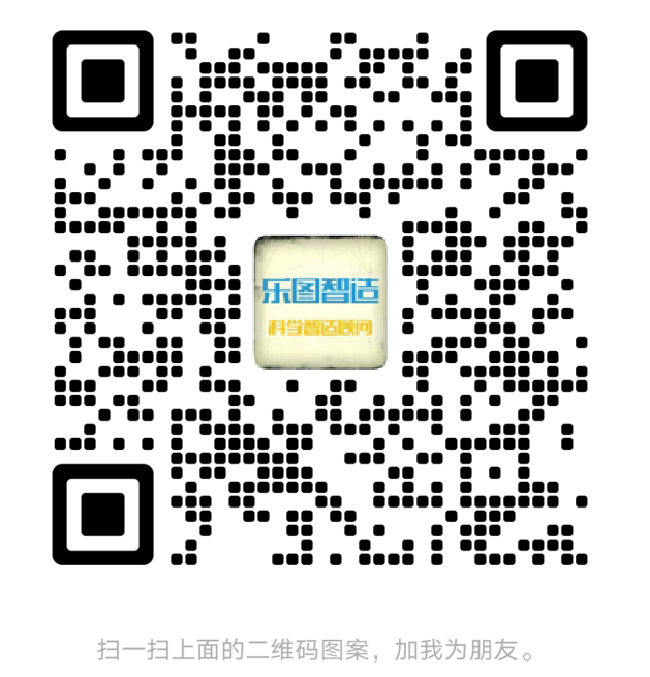
Leto Intelligent Manufacturing Technology (Suzhou) Co., LTD
199 4191 2022
Business consulting/technical consulting/exchange advice
Scan code wechat consultation, 24 hours to look forward to your voice