Biomedical stress analysis of anterior cruciate ligament
Senior engineers with over 10 years of experience, rich in practical experience in finite element analysis in the biomedical industry, having long-term cooperation with numerous medical equipment enterprises and medical research centers, and having obtained many patents in the research and development of medical equipment and the innovation of biomedical solutions.
Fields Involved in Biomedical Finite Element Analysis
· Orthopedic products · Medical fasteners · Eye modeling · Soft tissue simulation · Medical packaging · Medical electronic systems · Virtual biomechanics · Knee replacement · Human body modeling · Soft tissue and joint modeling · Hospital equipment · Laser welding · Ablation catheters · Dental implants · Mechanical connectors · Prosthetics · Pacemakers · Vascular implants · Defibrillators · Heart valve replacement surgery
Biomedical Stress Analysis of the Anterior Cruciate Ligament in the Human Body
Background: In biomedical mechanics analysis, sports and car accidents are important causes of ligament injuries, and the injury of the anterior cruciate ligament (hereinafter referred to as ACL) is the most common ligament injury. Among the many ligaments that hold the human knee joint together, the ACL is particularly important because it can maintain the stability of the knee and help prevent knee injuries by limiting joint movement. The ACL is mainly composed of densely packed collagen fibers connecting the femur and tibia. The ACL is located inside the knee joint, as shown in the following figure:
Biomedical Mechanics Analysis Working Conditions:
Working Condition One: A uniaxial displacement load is applied to the upper surface of the ACL, with a total elongation rate of 1.12.
Working Condition Two: The ACL is bent at 45 degrees (knee flexion).
Working Condition Three: Rotate the femoral surface by 11.25 degrees within 1.5 seconds.
Material Parameters and Finite Element Mesh Model:
The SOLID187 element is used for meshing. The femur uses a rigid surface. A standard contact (KEYOPT(12) = 0) is defined between the femoral surface and the ACL.
An anisotropic hyperelastic material model is used for the simulation of biomedical stress analysis of the ACL.
Boundary Conditions and Loads:
The tibial (bottom) side of the ACL model is kept fixed, and all degrees of freedom are constrained. The knee joint can be flexed, extended, and rotated. Therefore, this analysis examines the behavior of the ACL under uniaxial bending, tension, and rotation, which are the three working conditions of biomedical stress analysis.
Results of Biomedical Mechanics Analysis:
Working Condition One: Tension Working Condition
Working Condition Two: Bending Condition
Damage and tearing are prone to occur at the position of maximum stress.
According to research, the ultimate tensile strength of the Anterior Cruciate Ligament (ACL) is (2020 ± 264) N, and the maximum deformation is (15.9 ± 3.5) mm. The stiffness of the ACL is 240 N/mm, the elastic modulus is 278 MPa, and the ultimate tensile strength is 35 MPa [9]. The change in stress is related to the flexion and extension positions of the knee joint, the state of muscle contraction, and whether it is under load or not. Research on the material properties of the ACL cannot fully reflect the change in stress on the ACL under motion conditions. The stress change of the ACL varies under different magnitudes of external forces, flexion angles, and between different bundles. During flexion and extension movements, under the anterior-lateral forces of 110 N and 22 N on the tibia, the stress of the ACL is the greatest when the flexion angle is 15°, which is (110.6 ± 14.8) N and (25.7 ± 3.7) N respectively; when the flexion angle is 90°, the stress is the smallest, which is (71.1 ± 29.5) N and (12.8 ± 7.3) N respectively. The stress change during the flexion and extension process is also different under different constraints.
Working Condition Three: RotationWorking Condition
In daily activities, the maximum stress of the ACL is generally less than the ultimate stress, usually ranging from 0.0% to 44% of the ultimate stress. Under normal circumstances, when the quadriceps femoris mainly contracts and the flexion degree is relatively small (such as isometric contraction of the quadriceps femoris, squatting, active knee extension, etc.), the ACL bears greater force; while when the hamstring mainly contracts and the flexion degree is relatively large (such as isometric contraction of the hamstring, isometric contraction of the quadriceps femoris at 60° and 90°, and synergistic contraction of the quadriceps femoris and hamstring, etc.), the stress on the ACL is very small. In the early stage of the gait cycle (the process of the foot leaving the ground), the ACL experiences a relatively large shear force, and the maximum stress of 303 N occurs when the foot leaves the ground. In the later stage (the process of the foot touching the ground), due to muscle contraction, ground reaction, and the interaction between the tibia and femur, the force on the ACL is relatively small. Understanding the law of stress change on the ACL under physiological activities is of great significance for correct postoperative rehabilitation, avoiding dangerous positions and movements of the ACL, and preventing excessive loads.
Other Biomechanical Analysis Cases
The following figure shows a finite element mesh model constructed by using Mimics and Ansa with the foot pictures output by medical software, and the biomechanical analysis in medicine is solved in Abaqus.
Schematic diagram of the attachment points of bones and ligaments in the foot
Model loading and boundary conditions
Comparison between the predicted pressure center by the finite element method and the experimental measurement results
Stress nephogram of bones
The influence of different gait cycles when wearing high heels on the joints and ligaments of the foot
Declaration: This article is originally from the official website of Letu Zhizao. Please indicate the source when reprinting.
View more cases: Die Casting Mold Flow Analysis Modal Analysis Electromagnetic Field Simulation Analysis Drop Analysis Fatigue Analysis CFD Analysis
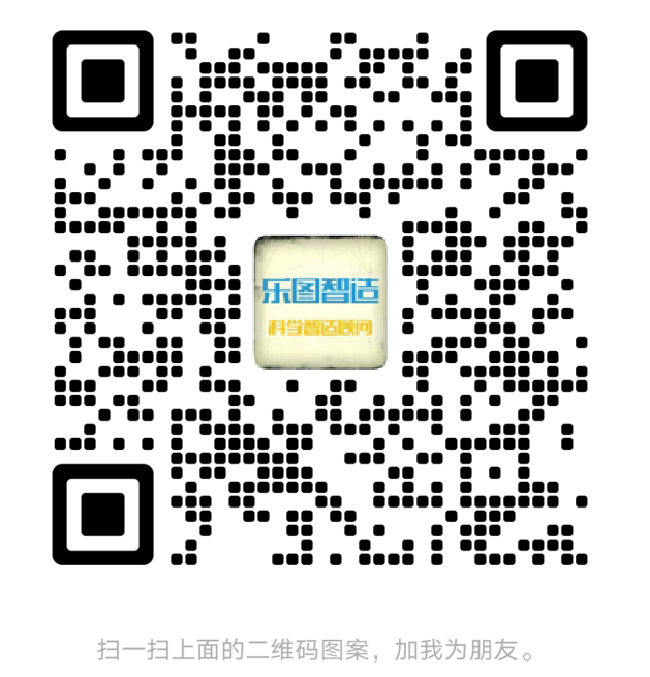
Leto Intelligent Manufacturing Technology (Suzhou) Co., LTD
199 4191 2022
Business consulting/technical consulting/exchange advice
Scan code wechat consultation, 24 hours to look forward to your voice