Simulation mold flow analysis of steering wheel micro-foaming molding
Contents of service:
Conduct microporous foaming mold flow analysis, IC chip packaging mold flow analysis, gold wire offset analysis, UDB material test fitting, and molding defect optimization.
Application value:
Microporous foaming mold flow analysis is a computer-based technology, which can help manufacturers optimize mold design, improve production efficiency and reduce production costs. In the manufacture of micro foaming products, the mold flow analysis technology has the following applications:
Optimized mould design
Die flow analysis can help manufacturers to simulate when designing dies, predict material flow and optimize die structure and dimensions. This can effectively reduce tests and errors in the mold design process and improve product quality and stability.
Prediction of surface defects
Due to the special structure of micro-foaming products, surface defects often affect the quality and performance of the entire product. Die flow analysis can accurately predict the location and type of surface defects through simulation, thereby helping manufacturers optimize die design and reduce product defect rate.
Improve production efficiency
With die flow analysis technology, manufacturers can optimize many parameters in the injection molding process, so as to improve production efficiency. For example, the packing speed, pressure, temperature and other parameters can be optimized to reduce the occurrence of excessive or insufficient materials, effectively reduce the scrap rate and increase the production efficiency.
Case - Steering wheel PU micro-foaming molding mold flow analysis
Forming conditions:
Product volume approx. 933cc. Under the setting of forming processing conditions, the filling volume percentage at the filling time of 3.5 seconds is 35%. The die temperature is set to 50 ° C and the PU material feed temperature is 25 ° C.
Microporous foaming mold flow analysis results: flow front time, density, temperature, conversion rate, foaming conversion rate, etc
Melt flow leading edge temperature
Figure (a) shows the filling area and Figure (b) shows the melt flow leading edge temperature at the end of foaming
When the filling reaches 35% of the cavity, the polyurethane reaction liberates CO2 gas and the viscosity of the polymer gradually increases due to the gel reaction. At the same time, the heat of reaction from the exothermic cure reaction will be released and cause an increase in cavity temperature. As a result, more and more CO2 gas is released into the polymer melt at relatively high temperatures. Eventually the PUR foaming melt will completely fill the cavity space. Temperature: As the foaming reaction will release a lot of heat, the temperature will increase with the increase of filling process time, but if the internal temperature is higher than the mold temperature, the temperature will be dissipated from the mold wall.
Polyurethane foaming density distribution
Figure (a) shows the filling area and Figure (b) shows the polyurethane foaming density distribution
The density distribution results show the expansion effect during foaming at 35% of the charge. The higher the foaming conversion, the more CO2 gas is produced. It results in a larger cell volume and lighter density for polyurethane foaming. As the foaming reaction takes place emitting a large amount of gas, the density becomes lighter and lighter as the filling process increases.
Foaming conversion rate and melt conversion rate
Melt conversion rate: the conversion rate represents the degree of chemical cross-linking reaction. The higher the conversion rate is, the closer the product is to be solidified, and the higher the temperature is, the faster the conversion rate is.
Foaming conversion rate: the foaming conversion rate represents the degree of chemical foaming reaction. The higher the foaming conversion rate is, the more gas will be generated. The higher the temperature is, the faster the foaming conversion rate will be.
Summary:
Through the microporous foaming mold flow analysis, the chemical foaming process of different products is simulated, the influence of foaming conversion rate and melt conversion rate can be known, the filling behavior in the molding process is simulated, the final product weight is predicted, the bubble size, number, density distribution and other results are estimated, and the weight reduction ratio of the product is evaluated.
Microporous foaming mold flow analysis involves the following fields:
Automobile industry: automobile parts, such as door panel, instrument panel, steering wheel, seat frame, etc.
Aerospace: Aircraft and spacecraft parts, such as hatches, wings, etc.
Electronic industry: enclosure and internal structural parts of electronic products, such as mobile phones, televisions, etc.
Sports equipment: such as sports shoes, snowboards, skateboards, bicycles, etc.
Packaging industry: packaging materials, such as pallets, cushions, etc.
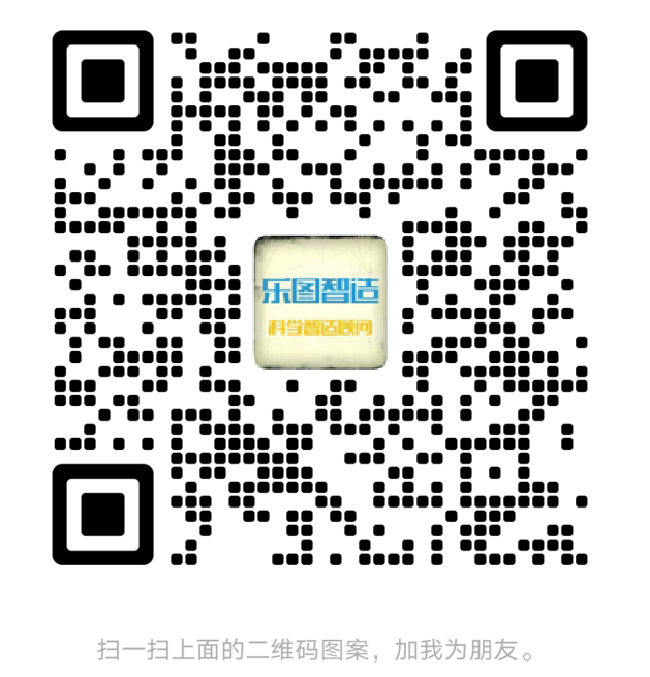
Leto Intelligent Manufacturing Technology (Suzhou) Co., LTD
199 4191 2022
Business consulting/technical consulting/exchange advice
Scan code wechat consultation, 24 hours to look forward to your voice