New energy vehicle battery pack heat dissipation simulation analysis
Business Content:
Thermal Management Engineering Consulting: Finite element analysis for thermal management development such as thermal simulation analysis of new energy battery packs, thermal analysis of electronic components, solar radiation analysis, etc.
With experience in over 100 project cases, reasonable charges, quick response, short delivery time, and reliable quality.
Application Value of Thermal Simulation Analysis:
Drive lean design and rapid development processes, which can save a lot of development costs and shorten the development cycle. The heat energy accumulated in the battery pack not only causes the battery to overheat but also may even pose safety risks. Therefore, in order to effectively dissipate the heat of the power battery pack of electric vehicles, ensure that each battery module operates within a suitable temperature range, and maintain the consistency of the temperature difference between each battery module, thereby improving the performance of the power battery pack, a cooling device must be adopted when designing the battery pack structure. Apply finite element analysis tools to optimize the design scheme.
Application Cases of Battery Pack Thermal Analysis:
Simulation Data Cloud Diagram 1 of Directional Explosion-proof Heat Simulation Analysis
The power battery is the energy source of electric vehicles. During the charging and discharging process, the battery itself will generate a certain amount of heat, resulting in a temperature rise. And the temperature increase will affect many characteristic parameters of the battery, such as internal resistance, voltage, SOC (State of Charge), available capacity, charging and discharging efficiency, and battery life. High temperature will greatly reduce the calendar life of the battery, thus affecting the performance and service life of the whole vehicle. Too low temperature will also cause the capacity of the power battery to decline and the charging time to be too long, thus affecting the performance of the electric vehicle. In the design of lithium battery packs, thermal-fluid simulation analysis is often used to assist engineers in completing the pack thermal management system design. With the help of thermal simulation analysis tools, most of the pack thermal management design work and some testing work can be completed on a computer. A large amount of design, manufacturing, and testing work can be omitted, and the cost of pack design will be greatly reduced.
Simulation Data Cloud Diagram 2 of Directional Explosion-proof Heat Simulation
The battery pack of the electric vehicle battery system usually consists of a large number of battery cells and connects multiple battery units in series or parallel to form the required voltage and capacity. Improving the performance of the battery pack is of great significance to electric vehicles. However, the performance of the battery pack is severely affected by the temperature uniformity of each cell within the pack. During the working process, there will be strong differences inside each battery module in the battery pack, resulting in an excessive temperature difference between each battery in the pack, thus enlarging the differences in battery resistance and capacity. The life and performance of the battery will also be adversely affected due to possible overcharging and overdischarging when it is in this working state for a long time. In addition, poor heat dissipation design of the battery pack will cause heat energy accumulation during charging and discharging.
Main Requirements of Battery Thermal Management System are as follows:
1. Avoid thermal runaway and ensure effective ventilation when harmful gases are generated. 2. Effectively dissipate heat in a high-temperature environment. 3. Quickly heat up or keep warm in a low-temperature environment. 4. Reduce the battery temperature difference and ensure the temperature uniformity of the battery. 5. Accurately measure and monitor the battery temperature.
There are two design goals for the power lithium battery thermal management system:
1. Maintain the interior of the battery pack within a reasonable temperature range; 2. Minimize the temperature difference between different battery cells.
The left figure shows the thermal distribution result of the battery pack, and the right figure shows the thermal cycle result of the cooling system. According to the simulation data of cooling fluid analysis, the cooling, heating, and heat preservation methods can be quickly selected; during the design stage of the cooling subsystem, thermal field and flow field simulation analysis can be carried out on the pack, module, or battery (with cooling subsystem). Based on the thermal simulation results, the design of the cooling channel, cooling medium, cooling inlet temperature and flow rate, as well as the parameters of the fan or pump can be determined. In the simulation process of power battery thermal management, the pre-processing technologies such as geometric cleaning, mesh generation, input of simulation boundaries and thermal management strategies, and battery modules are difficult points, especially for the electrochemical simulation of battery modules.
Optimization Direction of Cooling System Structure:
For the liquid cooling system, the working principle of the liquid-cooled plate is as follows: The excess heat generated by the battery operation is transferred through contact with the surface of the plate-shaped aluminum device. The liquid cooling system utilizes the characteristic of a large liquid flow heat transfer coefficient and relies on the liquid flow to transfer high heat, which is finally taken away by the coolant passing through the internal flow channel of the device. Here, the details of its size design, flow rate design, and cooling area design will not be elaborated. In order to ensure the temperature consistency of the system, the cooling structure design is continuously optimized using simulation tools and tests.
It can be optimized from the following aspects:
a) Optimize the manifold. b) Adjust the width of the cold plate. c) Adjust the internal flow cross-section of the cold plate. d) Adjust the diameter of the main pipeline. e) Adjust the diameter of the branch pipeline.
Charging Standards for Thermal Analysis:
The quotation is calculated according to the difficulty of specific projects. Since CAE analysis covers a wide range, there are differences in engineering and various test projects, and there are differences in the types of finite element analysis and their difficulty coefficients, so it is impossible to unify the prices of standard projects. Guided by customer needs, the most suitable product solutions are formulated and recommended for each customer. Integrity is emphasized, quality comes first, and we serve wholeheartedly to win trust.
Information Required for Quotation:
1. 3D model drawing file for thermal simulation analysis (UG, Solidworks, Pro/E, CATIA, step are all acceptable). A confidentiality agreement can be signed. If the drawing is inconvenient to send, relevant test part pictures are also acceptable. Our company will fulfill strict confidentiality obligations.
2. PPT document for test condition description, clearly stating the content to be tested, mainly including: boundary conditions, thermal simulation focus areas, part material list, thermal simulation report format requirements, etc.
3. Requirements for thermal simulation analysis software, finite element simulation technical requirements, delivery time requirements, etc.
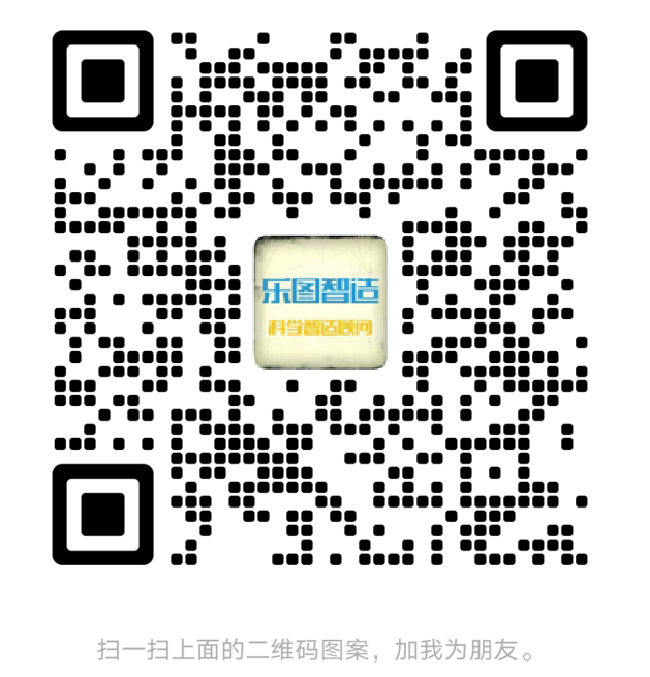
Leto Intelligent Manufacturing Technology (Suzhou) Co., LTD
199 4191 2022
Business consulting/technical consulting/exchange advice
Scan code wechat consultation, 24 hours to look forward to your voice