[Die casting program development] Aluminum alloy beam casting row design program development
Develop the Pouring and Venting Design Scheme for Aluminum Alloy Crossbeams Using the MAGMA Casting Simulation Software
Industry Background and Trends:
The requirement for vehicle lightweighting has led to the development of components in the directions of functional integration, weight reduction, and structural complexity. Currently, the development cycle requirements for components are becoming shorter and shorter. The traditional manufacturing and development of new products based on experience is more like a trial-and-error method. The scheme is optimized through multiple trial productions and verifications to improve product quality. This approach consumes a large amount of manpower, material resources, energy, and time, causing serious waste and no longer meeting the development needs of new projects.
Product Background and Requirements:
The basic dimensions of the casting are 416mm × 182mm × 22mm, with a mass of 4.45kg, and the material grade is ADC12. The overall wall thickness of this product is relatively uniform, with an average wall thickness of 4.3mm. Since the product needs to be assembled and welded, the requirements for porosity and profile tolerance are very high. According to the product's characteristics and quality requirements, an optimal gating system needs to be designed to ensure the sequential filling of the molten metal and minimize the flow porosity and gas porosity to the greatest extent. Meanwhile, there is a very large window area in the middle of the product, which poses a great obstacle to the filling of the molten metal. Therefore, great attention should also be paid to the forming state at the end of the product.
By using MAGMASOFT to visualize and make the development process transparent, and through comparative analysis of different process parameters and different process schemes, the best combination of process schemes can be obtained. This approach can predict the problems that will occur in the product in advance and implement improvement measures in the early stage of the scheme, thereby reducing the number of mold trials. Guided by the optimal scheme recommended by the software, the trial production was carried out. The results showed that the scheme, which originally required multiple trial productions and improvements, achieved the state of direct mass production after the T0 mold trial, maximizing cost savings and shortening the development cycle.
Figure 1: Four pouring designs (A to D) and the corresponding filling results at 75% filling
Evaluation and Selection of Gate Schemes:
The analysis and judgment of the four schemes are as follows:
Scheme A has a total of five gates, with evenly distributed gates and balanced pouring, enabling overall pouring. The pressure is also relatively evenly transmitted to ensure density. Attention should be paid to the filling area at the far end, where there is a risk of cold material accumulation, poor filling, and poor venting.
Scheme B has a total of three gates. The large-volume area of the product corresponds to large gates to ensure filling quality and pressure transmission. However, thick and large gates are likely to cause excessively high local temperatures, resulting in deformation and having a negative impact on the mold. Meanwhile, this placement will lengthen the filling stroke.
Scheme C has a total of three gates. The large-volume area of the product corresponds to large gates to ensure filling quality and pressure transmission. However, thick and large gates are likely to cause excessively high local temperatures, resulting in deformation and having a negative impact on the mold.
Scheme D has a total of three gates. The large-volume area of the product corresponds to large gates to ensure filling quality and pressure transmission. However, thick and large gates are likely to cause excessively high local temperatures, resulting in deformation and having a negative impact on the mold.
According to the set process conditions, after the software completes the calculations of the four schemes, multi-dimensional big data statistics are carried out. Based on the evaluation of the smooth flow of the aluminum liquid, Scheme A is recommended as the best pouring scheme.
Figure 2 Evaluation Results of Pouring Schemes
Selection of Venting System Schemes:
After determining the initial venting system, the flow simulation was carried out again, and it was found that the existing venting system was not perfect and there was high air pressure at the end of the product. The high-pressure area has a very high risk of large pores, which will seriously affect product forming, welding, and assembly. Therefore, the venting scheme was optimized according to the simulation results, and venting channels were added in the high-pressure area to reduce the risk of gas accumulation. In actual production, a vacuum process needs to be supplemented. Based on this process design, the simulation was carried out again, and the air pressure distribution of the product before and after optimization was observed and compared. It was found that after adding the venting channels and the vacuum process, the air pressure value in the original high-pressure area dropped from 5000 mbar to 1000 mbar, indicating that the high-pressure problem was effectively improved. See Figure 3 for details.
Figure 3 Comparison between the Optimization of the Venting System and the Optimization Simulation Results
After determining the pouring and venting system, it is also necessary to design and calculate the die-casting process parameters. The autonomous optimization tool of MAGMASOFT enables engineers to explore a larger design space more time-efficiently and labor-efficiently by understanding the impact of process variables on casting quality, and then find the optimal die-casting mold and process layout scheme. Different from traditional simulation, autonomous simulation only requires engineers to set up a simulation once. However, many simulation runs will cover the entire process window. The software autonomously selects possible designs, analyzes them, and summarizes all the results in a statistical manner.
DOE Optimization of Die-Casting Process Parameters:
Based on the completion of the pouring and venting system design, the die-casting process parameters are optimized with the help of the DOE autonomous optimization tool. The high-speed velocity is a key parameter that affects the filling of the aluminum liquid and product quality. Taking the DOE optimization process of the high-speed velocity as the research object for analysis, the high-speed velocity is set between 3.5 - 4.0 m/s, and the iteration step length is set to 0.1, with the goals of reducing the gate velocity and minimizing cold shut defects. After big data analysis and statistics by the software, the optimal forming process parameters are recommended. Selecting a high-speed velocity of 3.5 m/s can not only meet the requirement of a low gate velocity, reduce mold erosion, but also ensure product quality.
Through the standard process of the pouring scheme and parameter design of MAGMASOFT, the pouring and venting system design of the product and the optimization of the die-casting process parameters have been completed. Guided by this data, it is used for actual verification. For the first trial production, a 1600T die-casting machine was selected and supplemented with a vacuum system, and the trial production was carried out according to the die-casting parameters optimized by DOE. Figure 9 shows the casting diagram of the first trial. Through X-ray detection of the internal quality, it was found that the internal quality of the casting was relatively ideal, and internal quality defects such as pores, shrinkage porosity, and shrinkage cavities all met the standards of ASTM F_505 Level 1. After the product was verified by welding, no welding defects occurred in the welding area, proving that the internal gas content of the product was very low. The product was successfully trial-produced for the first time.
Taking the development process of the die-cast aluminum alloy crossbeam as an example, this article uses MAGMASOFT to visualize and make the development process transparent. In this way, the problems that will occur in the product can be predicted in advance, and improvement measures can be taken in the early stage of the scheme to reduce the number of mold trials. Through the DOE optimization of the pouring and venting system and die-casting process parameters of the crossbeam, and guided by the optimal scheme recommended by the software, the product achieved the state of mass production in the first trial production, maximizing cost savings and shortening the development cycle.
Contact for Consultation, Explore Scientific Casting Schemes, and Create Higher Added Value Together
Letu Zhizao Technology, Product Performance Optimization, Finite Element Analysis Engineering Services, Software Sales, Providing Scientific Numerical Information Technology Solutions,
Declaration: This article is originally from the official website of Letu Zhizao. Please indicate the source when reprinting.
View more cases: Lightweight Design Heat Dissipation Analysis of Battery Packs CFD Analysis Analysis of Shrinkage Porosity in Castings Die Casting Mold Flow Analysis Deformation Analysis of Castings Casting Simulation
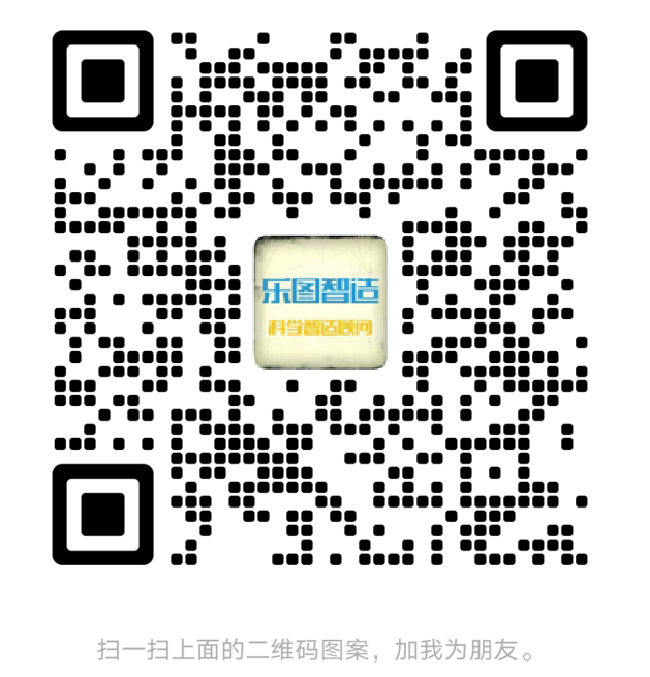
Leto Intelligent Manufacturing Technology (Suzhou) Co., LTD
199 4191 2022
Business consulting/technical consulting/exchange advice
Scan code wechat consultation, 24 hours to look forward to your voice