[Die casting shrinkage optimization] How to solve the shrinkage hole of aluminum alloy die casting?
Product Performance Optimization, Product Defect Optimization, 3D Scanning, Finite Element Analysis, Software Sales, Providing Scientific Numerical Information Technology Solutions for the Manufacturing Industry
How to Solve the Shrinkage Porosity and Shrinkage Cavity Problems of Castings? Solutions to the Shrinkage Porosity and Shrinkage Cavity Problems of Castings:
1. How to solve the shrinkage porosity and shrinkage cavity defects of aluminum alloy die castings? Apply the MAGMA analysis software to optimize the mold design scheme, improve the shrinkage porosity defects of castings, and enhance the quality of castings.
2. How to increase from 2 cavities to 4 cavities, double the die casting production capacity, and reduce the comprehensive cost.
Product Background:
This is an aluminum alloy lid part. The functional requirements demand the maximum operational reliability of the casting's structural strength and hydraulic seal to prevent oil leakage. Due to such high quality requirements, the internal compactness of the die casting becomes very important. Key considerations are needed in the mold design and manufacturing scheme to ensure that defects such as air holes and shrinkage porosity in the casting are as small as possible. This is both a challenge and an opportunity for mold manufacturers.
Requirements for the Mold Development Scheme:
Increase from 1 mold with 2 cavities to 1 mold with 4 cavities.
Minimize the shrinkage porosity in the thick area shown in the figure as much as possible.
Original Mold Development Scheme:
Shortcomings:
1. The number of cavities is small and the production capacity is low. Due to the product structure, the casting arrangement cannot achieve a completely balanced distribution of the runner system. The manufacturer was not confident enough, so a 1-mold-2-cavity scheme was adopted.
2. Due to the product functional requirements, the local thickness in the area indicated by the arrow in the above figure is relatively thick, which will lead to slow local solidification and shrinkage, resulting in casting defects such as shrinkage cavities and shrinkage porosity. In the existing runner system scheme, the gate position is selected on the side end face of the casting, as shown by the red circle in the above figure, which fails to effectively compensate for the shrinkage porosity problem.
Optimization of the Design Scheme:
How to Solve the Shrinkage Porosity and Shrinkage Cavity Problems of Castings? Solutions to the Shrinkage Porosity and Shrinkage Cavity Problems of Castings, Optimization Measures:
In response to the problem that the local thickness in the area indicated by the arrow in the previous picture is relatively thick, which will lead to slow local solidification and shrinkage and result in casting defects such as shrinkage cavities and shrinkage porosity, a gate is opened on its side, and the parting line of the casting is changed.
The positions of the castings are rearranged to make it a 1-mold-4-cavity design. The runner is designed to have the flow length as equal as possible. Then, through mold flow analysis, the runner size is verified and adjusted to make the filling of the 4 cavities reach the maximum balanced state.
For the position of shrinkage porosity, a cooling system is designed. (As shown in the figure below.)
Comparison of MAGMA Mold Flow Analysis Results:
Here comes the moment to witness the miracle. As shown in the shrinkage porosity results in the following figure, the shrinkage porosity is the most serious in the original scheme. After optimizing the gate position, the shrinkage porosity is reduced. With the additional strengthening of local cooling, the shrinkage porosity volume is significantly reduced. Thus, the shrinkage porosity problem of the casting is successfully solved.
Left: Original Development Scheme Middle: Optimized Scheme, with the gate position changed Right: Local cooling strengthened on the basis of the optimized scheme
Sample Comparison:
The tomographic scan analysis of the sample casting is very consistent with the results of the MAGMA analysis, once again proving the accuracy and reliability of the mold flow analysis.
This set of molds has been successfully developed. The yield rate of the castings is as high as over 99%. Coupled with the increase in the number of cavities to 1 mold with 4 cavities, it has added at least 500,000 yuan in profit for the customer. How to solve the shrinkage porosity and shrinkage cavity problems of castings? For solutions to the shrinkage porosity and shrinkage cavity problems of castings, please feel free to call for consultation.
Contact for Consultation, Explore Scientific Casting Schemes, and Create Higher Added Value Together
Letu Zhizao Technology, Product Performance Optimization, Finite Element Analysis Engineering Services, Software Sales, Providing Scientific Numerical Information Technology Solutions,
Declaration: This article is originally from the official website of Letu Zhizao. Please indicate the source when reprinting.
View more cases: Optimization of Shrinkage Porosity in Re-casting Lightweight Design Heat Dissipation Analysis of Battery Packs CFD Analysis Analysis of Shrinkage Porosity in Castings Die Casting Mold Flow Analysis Deformation Analysis of Castings Casting Simulation
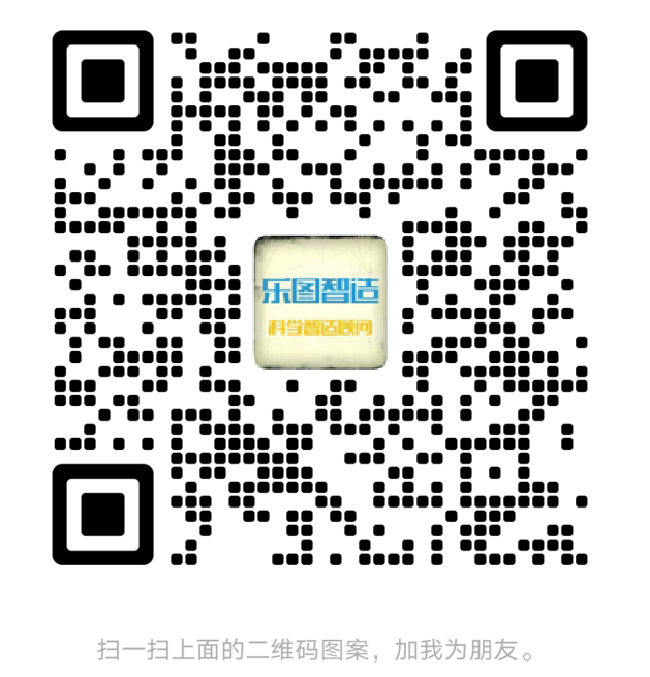
Leto Intelligent Manufacturing Technology (Suzhou) Co., LTD
199 4191 2022
Business consulting/technical consulting/exchange advice
Scan code wechat consultation, 24 hours to look forward to your voice