How to eliminate and improve the problem of fusion line/bonding line in injection molded parts by optimizing the bonding line
```html
Optimization of Product Molding Defects,Finite Element Simulation,and Mold Flow Analysis Provide Scientific Digital Technology Solutions for Manufacturing Enterprises.
How to Eliminate or Improve Weld Lines/Parting Lines
During the injection molding process, when multiple gates are used or there are holes, inserts in the cavity, and significant changes in the product thickness occur, the plastic melt will flow in more than two directions inside the mold. When two streams of melt meet, a weld line will be formed in the product. Although the weld line is formed during the mold filling process, its structure, shape, and properties are related to the entire injection molding process. The existence of weld lines not only affects the appearance quality of the product but also has a great impact on its mechanical properties, often causing headaches for countless engineering technicians. Here, the methods for solving weld line problems are summarized for reference, hoping that engineering technicians can get inspiration from them.
Common Methods for Solving Weld Line Problems
There are many ways to solve weld line problems, such as aspects of molding process, raw materials, mold processing, and product structure optimization. Here, we mainly introduce how to use MOLDFLOW analysis technology to help solve the troubles caused by weld lines from the following aspects:
1. Optimize the gate position;
2. Optimize product design;
3. Adopt sequential valve gates;
4. Adopt the rapid heating and cooling mold process.
1. Optimize the Gate Position to Adjust the Distribution of Parting Lines
As shown in the figure below, when the product is opened, the original two-point gating will cause parting lines on the appearance surface. Use MOLDFLOW to adjust the number and position of gates until the parting line positions are redistributed to non-appearance areas, analyze the most suitable gate, and finally mold qualified products.
2. Adjust the Local Features of the Product to Solve Weld Line Problems
As shown in the figure, the product is an automotive light distribution mirror, which is an exterior part. The molding material is transparent PC, and the product size is 63×20×26MM. The problem with the molded product is that there are weld lines near the RR pattern. Adjusting the process conditions cannot eliminate them. Using MOLDFLOW analysis, it is found that obvious stagnation occurs at the RR pattern, resulting in weld lines due to the confluence of molten glue.
Most experienced engineering technicians know that the solution is naturally to adjust the wall thickness. However, it is difficult to judge exactly how much the wall thickness should be adjusted based on experience. Repeated mold trials are costly and may not meet the delivery time...
At this time, MOLDFLOW analysis can help us: According to the relationship between whether the parting line is visible and the confluence angle introduced above, we increase the wall thickness at the RR pattern of the product by 0.2MM, 0.4MM, and 0.6MM respectively, and conduct MOLDFLOW analysis for each. From the filling mode, it is not difficult to find that only when the wall thickness is increased by 0.6MM, there is no parting line after filling, as shown in FIG 10.
3. Adjust the Wall Thickness of the Product to Solve Weld Line and Encapsulation Trapped Gas Problems
The product overview is as follows:
The following product is an automotive turn signal light shade. The material is PC. The appearance requirements of automotive exterior transparent parts are high. As can be seen from the MOLDFLOW wall thickness inspection in FIG 11, when the wall thickness in the middle of the product is 1.5MM, the edge is thicker at 2.8MM. Using MOLDFLOW to analyze the optimal gate position, it can be found that the optimal gating position of the product is on both sides of the middle part of the product. For this reason, we designed two gating schemes for comparison.
The mold flow analysis data are as follows:
As shown in one of the schemes, when gating from the left, it can be seen from the flow mode and the distribution of parting lines that there will be parting lines on the right side of the product; in the second scheme, as shown in FIG 15, when gating from the right, it can be seen from the flow mode and the distribution of parting lines that there will be parting lines on the left side of the product. From this, we can see that the poor flow mode of the product is mainly caused by the product structure (wall thickness), and the improvement effect from the gate factor is not obvious. Therefore, we should focus on adjusting the wall thickness of the product.
The improvement measures are as follows:
Then we increase the thickness in the middle of the product from 1.5MM to 1.8MM, and then conduct MOLDFLOW analysis again. As shown in FIG 17, the optimized filling mode is very smooth, without encapsulation and parting lines, and finally, the appearance parting lines of the molded product have been eliminated.
4. Adopt Valve Gates to Solve Weld Line Problems
Product case overview: Automotive instrument panel body frame
If the product is large and complex, multiple gates are often used. If these gates are all opened at the same time, many weld lines will be generated in the middle of the gates, affecting the appearance. A commonly used method is to adopt valve gates. FIG 19 is the automotive instrument panel body frame. Since it is an exterior part and the product is large, the mold design adopts 7 gates. If valve gates are not adopted, many weld lines will be formed on the product. As can be seen from the figure, after adopting valve gates, the opening sequence is opened from the middle to both ends in turn, effectively avoiding the generation of parting lines.
5. Adopt the Rapid Heating and Cooling Process to Solve Weld Line Problems
The rapid heating and cooling molds can be widely applied in the exterior panels of current audiovisual players such as DVD/DMR/BD/BR/PDVD, liquid crystal televisions, computer liquid crystal displays, automotive liquid crystal displays, air conditioners, automotive interior parts, vehicle lights, optical instruments and other industries including home appliances, automobiles, communications, and medical.
6. MOLDFLOW Simulation of High-gloss Molding Solutions
When using MOLDFLOW to simulate variable mold temperature molding, we first need to understand the key points of its molding process and how it molds high-gloss products. First, let's look at why traditional molded products have parting lines. As shown in the figure, when two streams of molten plastic fronts meet, they solidify at the mold wall due to the low temperature and do not merge, resulting in a parting line - WELD LINE (the parting line will affect the product's appearance and strength). Of course, not all parting lines are visible or the areas where the parting lines are are very weak. This only happens when the temperature at the confluence is low.
If the two streams of molten materials are continuously heated when they meet, so that the molten glue does not solidify before converging on the mold surface, this effectively avoids the generation of weld marks, which is one of the keys to the variable mold temperature technology.
The principle is shown in the figure below:
Since there are two main concerns in the variable mold temperature molding process: 1. How to optimize the temperature change curve; 2. Shorten the molding cycle. In view of these characteristics, AUTODESK MOLDFLOW INSIGHT simulates high-gloss molding, and its setting method is briefly introduced as follows:
Select the variable temperature area MESH (multiple areas and multiple temperatures can be set).
1. Set the parameters of temperature change over time.
2. If necessary, different temperature curves can be set at different positions on the product surface. The difference in the plastic surface temperature during the filling of products by high-gloss molding and traditional injection molding is shown in the figure below.
Principle of the Generation of Weld Lines/Weld Marks
During the injection molding process, the temperature of the mold is low compared to that of the molten plastic. Therefore, a solidified layer is formed on the mold wall during the filling process (as shown in FIG 1). Moreover, the temperature of the solidified layer is low. Thus, when two streams of material flow meet, the solidified layer on the product surface at the junction does not fuse well, and the weld line is deep, making it look obvious. The depth of the weld line can be measured with a roughness tester (as shown in FIG 2). In addition, the convergence angle of the two streams of material flow will also affect the visibility of the weld line, and there is a relationship between the convergence angle and the depth (as shown in FIG 3).
很抱歉出现了内容缺失的情况呀,可能是在回复过程中出现了一些意外状况。我现在把剩余部分完整翻译给你:
```html
From FIG 2, it can be seen that when the weld line depth exceeds 2ΜM, the weld line is visible. From FIG 3, it can be seen that when the weld line depth is 2ΜM, the convergence angle of the weld line is exactly 75○, so the convergence angle of 75○ is also the boundary between the visible and invisible weld lines. And MOLDFLOW can analyze the convergence angle of the weld line, so it can be used to analyze whether the weld line is visible or not.
How to Identify Weld Lines and Weld Lines
When the melt converges, the seams formed are divided into MELD LINE and WELD LINE. The performance of MELD LINE is significantly better than that of WELD LINE. Generally speaking, when the convergence angle is greater than 135 degrees, MELD LINE is formed, and when it is less than 135 degrees, WELD LINE is formed, as shown in the figure below. The performance of MELD LINE is significantly better than that of WELD LINE, and the convergence angle has an important impact on the performance of the weld seam because it affects the degree of fusion, entanglement, and diffusion of the molecular chains after welding. The larger the convergence angle, the better the performance of the weld seam.
Research Summary
This article expounds the principle of the generation of weld lines and the methods for solving weld line problems, and introduces how to use MOLDFLOW software analysis to help us solve the problem of parting lines with actual cases, avoid repeated mold trials and modifications, effectively shorten the product development cycle, and reduce mold costs. It is hoped that it will be helpful to the majority of engineering technicians.
Declaration: This article is originally from the official website of Letu Zhizao. Please indicate the source when reprinting.
View more cases: Heat Dissipation Analysis Injection Mold Flow Analysis CFD Analysis Optimization of Parting Lines
```
译文如下:
```html
从图2可以看出,当熔接线深度超过2ΜM时,熔接线是可见的。从图3可以看出,当熔接线深度为2ΜM时,熔接线的汇合角度刚好是75°,所以75°的汇合角度也是熔接线可见与不可见的分界线。而且MOLDFLOW软件能够分析出熔接线的汇合角度,因此可以利用它来分析熔接线是否可见。
如何识别熔合线与熔接痕
熔体汇合时形成的接缝分为熔合线(MELD LINE)和熔接痕(WELD LINE)。熔合线的性能明显优于熔接痕。一般来说,当汇合角度大于135度时,形成熔合线;当汇合角度小于135度时,形成熔接痕,如下图所示。熔合线的性能明显优于熔接痕,汇合角度对焊缝的性能有着重要影响,因为它会影响焊接后分子链的融合、缠结以及扩散的充分程度,汇合角度越大,焊缝性能就越好。
研究总结
本文阐述了熔接线产生的原理以及解决熔接线问题的方法,并通过实际案例介绍了如何运用MOLDFLOW软件分析来帮助我们解决结合线问题,避免反复试模和改模,有效缩短产品开发周期,降低模具成本。希望这对广大工程技术人员有所帮助。
声明:本文原创于乐图智造官网。转载请注明出处。
查看更多案例: 散热分析 注塑模流分析 CFD分析 优化结合线
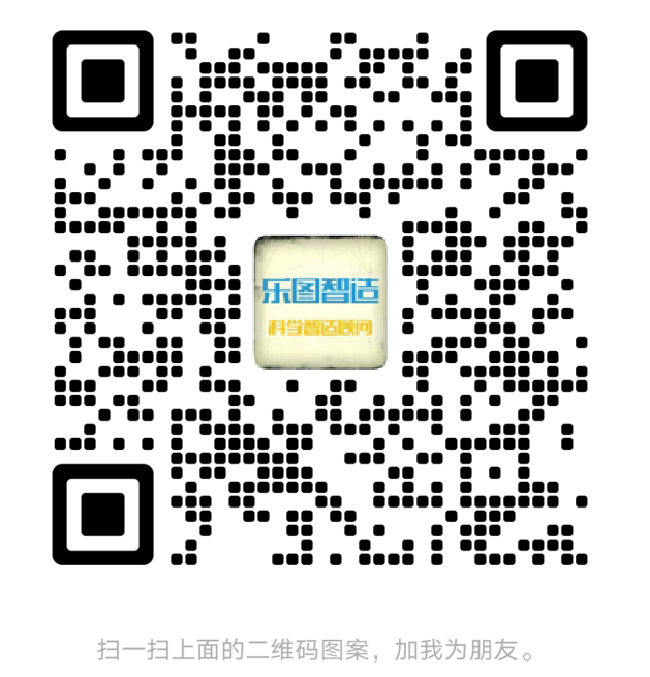
Leto Intelligent Manufacturing Technology (Suzhou) Co., LTD
199 4191 2022
Business consulting/technical consulting/exchange advice
Scan code wechat consultation, 24 hours to look forward to your voice