Lightweight design and development: The game between strength and weight optimizes product design
业务内容:
承包轻量化、强度优化、密封性优化、散热优化等产品设计优化工程
轻量化工程整包→从产品优化设计→cae分析验证→样板加工→开模具→小批量生产,一站式解决方案,各环节衔接更到位。
轻量化工程应用案例:
2021年一款电力设备塑胶产品,从产品优化设计→cae分析验证→样板加工→模流分析与模具设计→模具制造→小批量生产,由我司提供一站式解决方案,产品成功减重15%。国际上经济形势影响,竞争越来越激烈,由此背景下,有很多企业想尽一切办法节省制造成本,其中轻量化就是一个有效的方向,在满足产品各项功能基础上,减轻产品重量,这样就能节省出非常可观的一笔产品材料成本。
轻量化设计项目案例2::
主要目的:通过结构的最优化设计,在满足性能要求基础上重量最轻化。
轮式挖掘机的铰接杆在于前后连接、支撑各动臂,从而支配挖斗的挖掘、装车等动作。作为连接结构,需要满足刚度、强度、耐久性要求。传统上一般采用保守设计,存在较大的优化潜力。本文通过SIMULIA系列软件对铰链杆进行性能分析,结构优化和参数优化。
步骤一、 有限元分析测试性能
性能分析包括:强度分析和疲劳分析,其中强度分析使用ABAQUS软件,疲劳分析使用fesafe软件进行。
涉及有限元软件:ABAQUS、FEsafe、Tosca、Isight
1.1 强度分析测试条件(按照图所示施加载荷和边界条件。)
1.1.1强度分析结果
从分析结果来看,最大应力发生在后连接轴位置。
1.2 疲劳分析结果
将1.1中ABAQUS强度分析结果导入到fesafe中,载荷正负循环定义为一次。材料为SAE-1025。
从分析结果来看,最小疲劳寿命位置在后连接轴处。
步骤二、无参形状优化
2.1Tosca形状优化:
设计变量:选择疲劳寿命最小的位置处的节点作为形状优化的设计区域
设计目标:疲劳损伤最小
制造约束:相关位置自由度约束
Perform parameter-free shape optimization based on fatigue life performance, and use Tosca as the optimization software. The optimization process requires the combination of ABAQUS and fesafe to conduct strength and fatigue analyses.
2.2 Results of Parameter-free Shape Optimization Analysis
It can be found from the results of shape optimization analysis that when the nodes in the design area undergo free shape changes, the fatigue damage in the design area and the area of the connecting shaft position is constantly decreasing. The shape optimization results can effectively guide the shape optimization of the structural fatigue life.
2.3 Redesign the Structure According to the Shape Optimization Results to Improve Local Stress and Fatigue Performance.
2.4 Results of Strength and Fatigue Analyses After Optimization
From the analysis results, the fatigue performance has been improved by approximately 49%.
Step Three: Product Topology Optimization
3.1 In the product conceptual design stage, obtain innovative structural design schemes through the forward development process. Make the product lightweight while meeting the performance requirements, and then realize simulation-driven design. In this example, structural optimization is carried out with the initial design as a reference.
Design variables: Unit density of the design area.
Design constraints: Volume fraction ≤ 0.5.
Design objective: Minimum compliance.
Manufacturing constraints: Draft direction, minimum member size, symmetry constraints.
3.2 Model Reconstruction Design and Modeling
3.3 Results of Model Reconstruction Analysis
The topology optimization analysis obtains the optimized force transmission path. The volume of the retained material is related to the required structural mechanical properties at that position. However, the interpretation of the topology optimization has a certain degree of subjectivity. And in this example, the topology optimization takes minimizing compliance as the design objective and the volume fraction as the design constraint, which is not directly related to performances such as strength and fatigue. Judging from the analysis results of the reconstructed topology optimization model, both strength and fatigue are better than the original design.
Step Four: Shape Parameter Optimization Again (Based on the above analysis, there is still room for lightweight optimization of the structure.)
It has been mentioned in the section of topology optimization analysis that the volume of the retained material in the results of topology optimization is related to the required performance characteristics. If more material is retained, the performance requirements such as the sectional moment of inertia at that position are higher than those at the positions with less retained material. However, the interpretation of the topology results has a certain subjective influence. Therefore, it is necessary to continue the optimization analysis based on performance parameters.
4.1 Comparison of Products Before and After Optimization
4.2 Comparison of Analysis Results Before and After Optimization
4.3 Summary of Lightweight Design
Conduct performance analysis, structural optimization, and parameter optimization on the hinge rod. Explore to carry out the optimal design of the structure. Perform lightweight optimization design on the basis of meeting the performance requirements. Finally, the strength performance and fatigue performance have been improved, with a weight reduction of about 52 kg and a weight reduction ratio of approximately 30%.
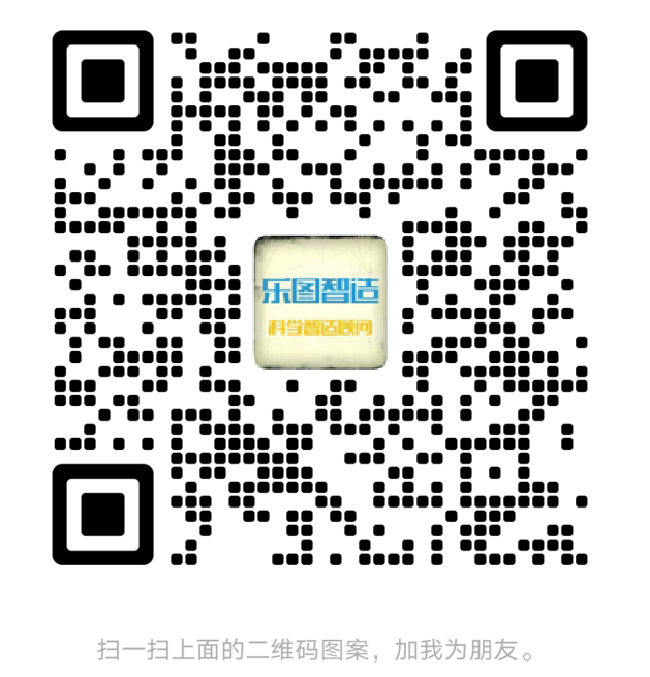
Leto Intelligent Manufacturing Technology (Suzhou) Co., LTD
199 4191 2022
Business consulting/technical consulting/exchange advice
Scan code wechat consultation, 24 hours to look forward to your voice