[Increase mold life] Combined with 3D printing technology +magma casting simulation technology, castings achieve twice the service life
Product Performance Optimization, Product Defect Optimization, 3D Scanning, Finite Element Analysis, Software Sales, Providing Scientific Numerical Information Technology Solutions for the Manufacturing Industry
Combining 3D printing technology + MAGMA casting simulation technology, optimizing the die-casting insert scheme, the service life of the casting has been doubled,.
It is an excellent case of applying the concept of intelligent manufacturing in science. It explains that in the face of the demand for high-quality and high-yield die-casting parts and the high cost of die-casting molds, in many products, as the surface of the inserts gradually ages, the local cooling effect on the casting is gradually weakened, which then leads to shrinkage holes in local parts of the product in subsequent production, and the scrap rate of product leakage testing is as high as more than 30%. In order to ensure product quality, these inserts often have to be replaced after 20,000 - 30,000 moldings, resulting in an increase in production costs. Based on the analysis of MAGMASOFT results, the goal is to design new cooling channels to improve the life of the inserts while improving production efficiency.
Considering that the material properties of the inserts remain basically unchanged, what changes is the transfer coefficient between the aged surface and the casting, that is, HTC. On the premise that all other conditions are the same, different interfacial heat transfer coefficients are set between the inserts and the casting. Through comparison, it is found that as the interfacial heat transfer coefficient decreases, the temperature of the insert body also decreases.
With the help of advanced 3D printing technology, break through the limitations of traditional CNC machining of cooling water channels, and ensure the rapid cooling of the inserts through conformal cooling and expanding the heat dissipation area of the cooling water channels.
Designs of different cooling channels: CNC traditional inserts (left), 3D printed inserts (right)
Even as the inserts gradually age (the interfacial heat transfer coefficient decreases), the temperature of the 3D printed inserts is nearly 50 °C lower than that of the traditional inserts. This shows that the cooling effect of 3D printing is much better.
X-ray inspection of castings: the left is the original casting, and the right is the casting after optimizing the inserts
In practice, after adopting 3D printed inserts, the product quality has been significantly improved, shrinkage hole defects have been greatly reduced, and the scrap rate has dropped to below 2% after leakage testing. Meanwhile, the service life of the inserts has been increased by 50,000 - 60,000 moldings. Based on the simulation of MAGMASOFT, the design progress of mold cooling conditions can be accelerated to ensure the effectiveness of the design.
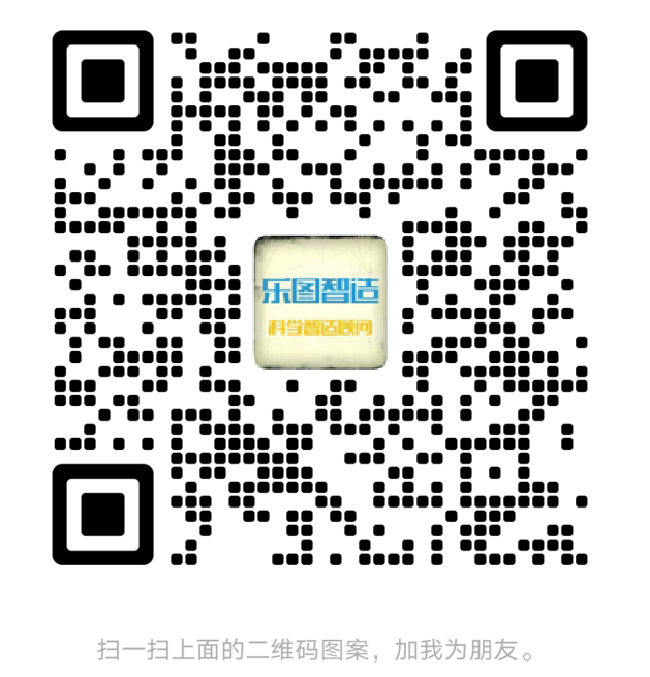
Leto Intelligent Manufacturing Technology (Suzhou) Co., LTD
199 4191 2022
Business consulting/technical consulting/exchange advice
Scan code wechat consultation, 24 hours to look forward to your voice