[Trapped gas burning] How to solve the trapped gas problem of injection molding products?
Product Performance Optimization, Product Defect Optimization, 3D Scanning, Finite Element Analysis, Software Sales, Providing Scientific Numerical Information Technology Solutions for the Manufacturing Industry
One of the Common Injection Molding Defects - How to Solve and Eliminate the Air Trapping Problem in Injection Molded Products? Applying Moldflow Cavity Pressure Analysis to Optimize the Design Scheme
Product Overview: The following figure shows a power plug product, which has a relatively thick overall thickness.
Product Problem Points: Short shot (incomplete filling), air trapping
Solution: Use Moldflow filling analysis to evaluate the causes of air trapping formation, and use Moldflow cavity and air pressure analysis to find the optimal exhaust position and the size of the exhaust groove.
1. Use the results of Moldflow air trapping pressure analysis to infer the causes of air trapping.
2. Apply Moldflow cavity and gas pressure analysis to determine the most suitable size of the exhaust groove.
3. Conduct mold modification and sample tracking, and finally the air trapping problem is completely solved.
The exhaust design of injection molds is very important. Poor exhaust can bring many problems, and the consequences can be said to be quite serious. In actual mold trials, we will find that air trapping and weld lines often occur simultaneously. Therefore, it is particularly important to predict the possible air trapping positions in the cavity in advance. Using Moldflow flow analysis in the early stage of mold design to check the flow pattern of the cavity, predict the air trapping positions, and even calculate the size of the exhaust groove is convenient and effective for optimizing mold design and reducing the troubles caused by air trapping.
Detailed Explanation of Common Causes of Air Trapping and Improvement Methods:
I. Hazards of Air Trapping in Injection Molds
The exhaust problem is a problem that cannot be ignored in the design of injection molds. If the exhaust is poor, it will cause many molding defects, such as short shot, burn marks, air holes, cavities, bubbles, surface silver streaks, weld lines and other obvious appearance problems. In many factories nowadays, the general practice is to add exhausts at the problem areas when encountering problems such as short shot or/and burn marks during mold trials. Even so, the exhausts are not added appropriately enough, leaving latent problems and resulting in excessive waste and high costs in the entire production process.
II. The main sources of air trapping in molds are as follows:
1. The air existing in the feeding system and the cavity.
2. The water vapor generated by the evaporation of the moisture contained in the plastic under high temperature.
3. The gas generated by the decomposition of the plastic.
4. The gas generated by the volatilization or chemical reaction of certain additives in the plastic.
5. The air and moisture mixed in the feeding.
III. Brief Introduction of Practical Cases, Problems of Color Change, Burn Marks and Cavities Caused by Insufficient Exhaust
Case 1: White spots on the transparent tube cap due to air trapping at the top
When the melt front traps the gas somewhere in the cavity, if the gas cannot find a way out, it will heat up under the high pressure pushed by the melt, and the melt front in contact with the high-temperature gas will be oxidized, degraded, discolored, or even burned and short shot. Figure 1 shows a transparent tube cap with white spots due to the oxidation, degradation and discoloration of the melt in contact with the high-temperature gas because of air trapping at the top.
Case 2: Rearview mirror of an automobile
Burn marks were generated at the filling end (last filled area) due to no exhaust path. The rearview mirror of an automobile generated burn marks at its filling end due to no exhaust path, and the corresponding Moldflow analysis results of air trapping.
Case 3: There are holes on the side wall of the polypropylene (PP) plastic part of a washing machine
On the side wall of the polypropylene (PP) plastic part of a washing machine, the injection speed was reduced due to air trapping to avoid burn marks. However, once the injection speed was reduced, the melt front cooled down and solidified, resulting in short shot and cavities.
IV. Brief Introduction of Practical Cases, Gas Mark Problems Caused by Insufficient Exhaust
Even if the gas in the cavity has a way to escape under the advancement of the melt front, if the passage (such as a gap) is too narrow, the aforementioned problems will still occur. Figure 4 shows a battery pack made of polycarbonate (PC). Although a perimeter vent was added at the parting surface of the cover edge, the depth of the exhaust lip was too shallow - only 0.01mm. Under high-speed injection, the gas could not escape in time and still formed gas marks at the cover edge.
There are obvious gas marks on the cover edge of the polycarbonate battery pack.
V. Brief Introduction of Practical Cases, Poor Weld Line Problems Caused by Insufficient Exhaust
The general countermeasure for dealing with insufficient exhaust is to reduce the injection speed. However, reducing the injection speed may lead to serious consequences such as short shot as shown in Figure 3. Even if the cavity is barely filled, there will still be several quality-affecting problems: 1. When forming a weld line, since the melt front has cooled down and the gas between the converging fronts has no time to escape, it blocks the fusion of the converging fronts, so the weld line is more obvious and fragile.
Case 1 Illustration: There are four obvious weld lines on the front cabinet of an ABS DVD player, marked with blue circles.
Reasoning:
For the front cabinet of an ABS DVD player (DVD player front cabinet), since its mold has no exhaust, there will be short shot or burn marks at the filling end under the normal injection speed. So a slower injection speed was adopted - the injection time was as long as 9 seconds. As a result, the melt cooled down while flowing, and when the two melt fronts were about to form a weld line, it was already too cold to make the two converging melts fuse more completely, resulting in a poor weld line as shown in the figure.
The poor weld lines downstream of the three round holes on the front cabinet of the DVD player are marked with blue circles.
Reasoning:
When two melt fronts form a weld line, the smaller the meeting angle between them, the more difficult it is for the gas between them to be removed. Figure is a short shot photo of a mouse base. The meeting angle between the two melt fronts forming a weld line is 40 degrees. This angle is too small and the weld line is more obvious. The acceptable meeting angle varies depending on materials, products and quality control specifications. Each factory should determine the acceptable minimum meeting angle through mold trials and experiments and use it as a standard for future designs.
Case 2: The meeting angle between the two melt fronts forming a weld line on the mouse base is 40°.
Case 3: The weld line on the edge of the oval window of the socket cover
A partial view of the ABS socket cover. The oval window is formed by the abutment of the entire male and female mold cores. When the cavity is filled, two melts converge on the left side of the window to form a weld line. The weld line closes at the window edge, but the gas driven to the closing position cannot find a way out, causing the weld line to oxidize and degrade, resulting in a large difference in color from the surrounding plastic. Therefore, an exhaust must be added at the closing position of the weld line at the window edge, and the gas should be guided out of the mold by drilling or mold inserts.
Case 3: The weld line on the edge of the oval window of the socket cover
A partial view of the ABS socket cover. The oval window is formed by the abutment of the entire male and female mold cores. When the cavity is filled, two melts converge on the left side of the window to form a weld line. The weld line closes at the window edge, but the gas driven to the closing position cannot find a way out, causing the weld line to oxidize and degrade, resulting in a large difference in color from the surrounding plastic. Therefore, an exhaust must be added at the closing position of the weld line at the window edge, and the gas should be guided out of the mold by drilling or mold inserts.
Case 4: The weld line problem on the S-shaped lampshade
The exhaust system from the cavity to the outside of the mold should be kept unobstructed. The figure shows a polycarbonate (PC) S-shaped lampshade mold. Its injection vents are spaced at 25mm intervals, with the exhaust lip being 0.04mm deep, 5mm wide and 1mm long, and the downstream exhaust groove being 1mm deep. All these are quite standard and impeccable. However, the bridge runner between the cavities and the pressure plate outside the mold block the exhaust passage, making the exhaust incomplete and resulting in the unpleasant weld lines as shown in the figure.
VI. Warpage Deformation Caused by Insufficient Exhaust
When the injection speed cannot be increased to the optimal point due to insufficient exhaust, the filling time will be prolonged. At the moment when the cavity is filled, in addition to a large temperature difference of the melt between the gate end and the filling end, the pressure drop is also large, and the difference in volumetric shrinkage will become larger accordingly, increasing the possibility of warpage deformation. The figure shows the PC upper cover of a thin-walled laptop. Its flatness does not meet the requirements due to the adoption of a long injection time. The flatness has been improved after the injection time is shortened from 7 seconds to 2 seconds.
The upper cover of the thin-walled laptop does not meet the flatness requirements.
VII. Long Molding Cycle Caused by Insufficient Exhaust
The molding cycle is the sum of the filling time, the holding pressure time, the cooling time and the mold opening time. Although the prolongation of the filling time due to insufficient exhaust will increase the molding cycle, the real reason for the extension of the molding cycle is often the extension of the cooling time, which makes the plastic parts forced to be shaped in the mold cavity cool down until their strength is sufficient to suppress the residual stress inside them. A considerable amount of this residual stress comes from the high shear stress caused by poor exhaust, reduced injection speed and cooling of the melt. Figure 12 shows two products and their runners from one of the hot nozzles in a two-hot-nozzle, four-cavity automotive seat POM female screw mold. The original design of the product has a large residual stress, and the molding time has to be extended to 112 seconds before the mold can be opened and the products ejected. The improved design reduces the residual stress, and the molding time is shortened to 68 seconds.
Two products and their runners from one of the hot nozzles in a two-hot-nozzle, four-cavity automotive seat female screw mold
VIII. Key Points for Basic Mold Exhaust Design:
1. Ensure that the exhaust is rapid and complete, and the exhaust speed should be adapted to the mold filling speed;
2. Try to open the exhaust groove at the thicker molded parts of the plastic parts;
3. Try to open the exhaust groove on the parting surface;
4. Try to set the exhaust groove at the end and the confluence of the material flow, such as the end of the cold slug well;
5. For the convenience of mold manufacturing and mold cleaning, the exhaust groove should be set on the side of the female mold as much as possible;
6. The direction of the exhaust groove should not face the operation surface to prevent material leakage and injury during injection molding;
7. The exhaust groove should not have sharp corners to prevent the accumulation of cold materials;
8. The size of the exhaust groove must be appropriate (generally with a thickness of about 0.2 - 0.3mm), and it should be selected and processed according to specific materials and product requirements, and try to avoid burrs as much as possible.
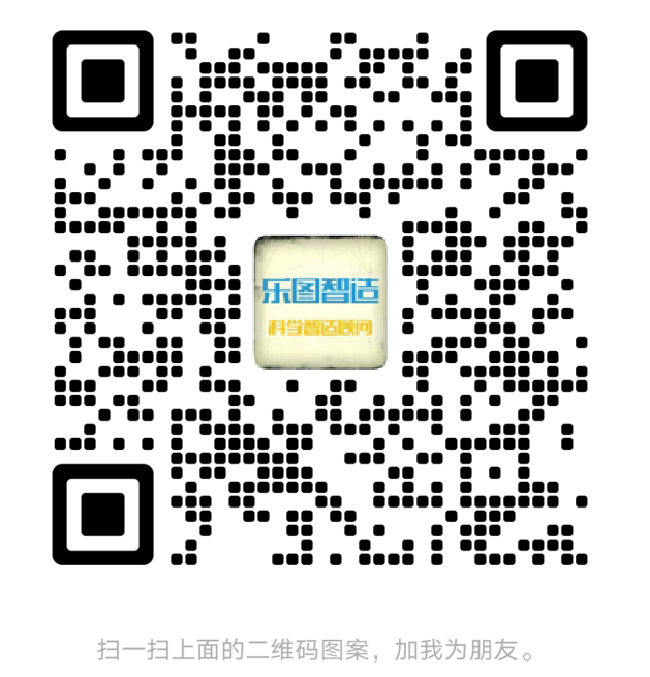
Leto Intelligent Manufacturing Technology (Suzhou) Co., LTD
199 4191 2022
Business consulting/technical consulting/exchange advice
Scan code wechat consultation, 24 hours to look forward to your voice