Lightweight Design and Development: Optimization of Weight Reduction for Components of Precision Punching Press Frame
Overview of Lightweight Design and Analysis:
Lightweight design is an eternal topic in structural design. Taking automobiles as an example, not only traditional fuel vehicles need to consider fuel economy and whether carbon emissions exceed the standard, but new energy vehicles also have to maximize lightweight design out of consideration for driving range. If the weight of the entire vehicle is reduced by 10%, fuel efficiency can be increased by 6% - 8%. For every 100 kilograms reduction in the curb weight of an automobile, CO2 emissions per kilometer will be reduced by 8.5 kg. Similarly, with the rapid development of the aerospace industry and the intensification of homogeneous competition in the traditional equipment manufacturing industry today, improving the overall performance of new products, reducing production costs, and shortening the R & D cycle have become the unremitting goals pursued by designers.
Technical Advantages:
We possess rich experience (over 100 sets) in lightweight design and analysis. Advanced topology optimization technical tools have been introduced. By defining material properties, load conditions, and constraint conditions, we seek the optimal distribution form of materials within a given design domain, greatly shortening the project development cycle in the early design stage and optimizing the structural design on the premise of meeting performance goals.
Successful Cases of Lightweight Design and Analysis:
Case Background:
This is the 12,000 kN fine blanking press frame produced by a certain company. The frame is welded with Q235-A steel plates of different thicknesses (ranging from 30 mm to 390 mm) and undergoes overall annealing treatment. The frame has to bear all the working loads, so its mechanical properties directly affect the working performance of the whole machine. On the other hand, the frame is large in size and consumes a lot of materials. It usually accounts for about 60% of the weight of the whole machine, and its structural lightweight design is of great significance for the lightweight design of the whole machine and the reduction of production and transportation costs. Therefore, it is necessary to conduct structural optimization design for the frame of the fine blanking press.
Performance Requirements:
1) It should have good structural strength, and the maximum working stress should be within the allowable stress range.
2) It should have good overall stiffness, and the overall stiffness can be measured by the structural strain energy or compliance under the rated load.
3) It should have sufficient local stiffness, that is, the deformation of the force-bearing surface and the guide surface (as shown in Figure 1c, due to symmetry, only two guide surface positions are marked) should be within the specified range.
4) It should have good dynamic characteristics, and the natural frequency of the frame should be far away from the excitation frequency to avoid resonance.
Overview of the Optimization Process:
Details of the Optimization Process:
Summary of Lightweight Design and Analysis:
1. Structural optimization design has been carried out for the 12,000 kN fine blanking press frame, and a new frame structural design form has been obtained. Compared with the original frame structure, the optimized frame structure has achieved a 13% weight reduction while improving performance, successfully realizing lightweight design.
2. By analyzing the structural characteristics of the optimized frame through finite element analysis, two conclusions have been drawn:
First, the top of the frame is designed in an arc shape, which is conducive to saving materials and reducing production and manufacturing costs while ensuring mechanical properties.
Second, the material distribution is close to the constraint parts and has a low center of gravity, which is beneficial to improving the dynamic performance of the structure.
Declaration: This article is originally created by Letu Zhizao official website. Please indicate the source when reprinting.
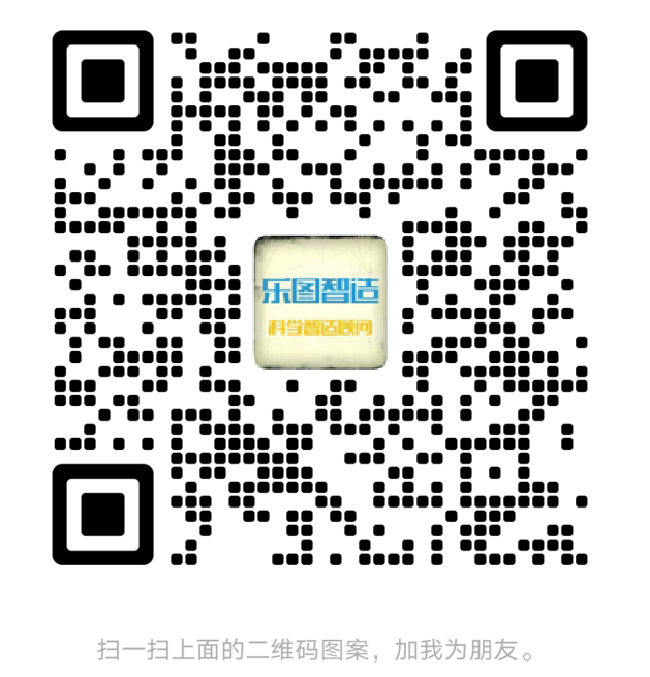
Leto Intelligent Manufacturing Technology (Suzhou) Co., LTD
199 4191 2022
Business consulting/technical consulting/exchange advice
Scan code wechat consultation, 24 hours to look forward to your voice